First Clean-Sheet Turboprop Engine Produced in 50 Years
GE's new, clean-sheet turboprop engine broke new ground Thursday, making its first successful flight on a King Air test bed. Flying out of Berlin Airport, the 1 hour and 40 minute jaunt added another important milestone to the design's continued development.
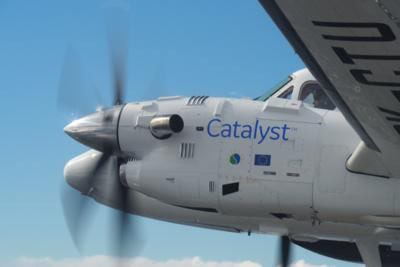
To date, 16 test engines have racked up over 2,600 hours of operation in ground tests and appear on track to continue a streak of promising performance. Dubbed "Catalyst", the engine will find its first home in launch customer Textron's (Cessna) Denali for further testing.
This is exciting news for aviation enthusiasts, being the first turboprop designed from scratch to reach the market in more than 50 years. The legendary Pratt & Whitney PT6, the Catalyst’s prime competition, completed its equivalent first flight on May 30, 1961. Since then, engineers have found it increasingly difficult to extract more performance out of less fuel with each passing year. These diminishing returns prompted GE to approach the drawing table and build the next generation’s power plant.
Including modern technology from the outset allows for a more compact, lightweight engine that will have an even longer market lifespan than previous competitors. Decreased weight results in a wider array of possible customers and aircraft applications, bringing much-needed cost savings as the user base expands. GE particularly looks to electric propulsion as aviation moves towards alternative power sources. Riccardo Procacci, CEO of Avio Aero and GE Turboprop Engines, described the Catalyst as "a super-efficient core that can pave our way towards hybridization of flight". An example can be seen in use with fellow GE partner XTI Aircraft. Their TriFan600 uses a single Catalyst to power three electric generators, with no direct linkage to a propeller. Their development roadmap shows the possibility of alternative fuels for lower emissions and greater sustainability as well as on-board battery or solar power.
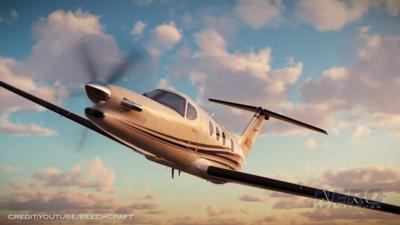
Unlike past engines, modern tech requires no retrofitment, having modern amenities baked in from the start. Of particular note is the Full Authority Digital Engine and Propeller Control (FADEPC) that grants a single lever integrating power and propeller control. Simone Castellani, one of the lead engineers to develop the system, described the result as so easy “my mom could do it. In a way, it’s just like flying a scooter.” With final power output aimed at the 850-1600 SHP range, the Catalyst features a 16:1 overall pressure ratio that enables lower fuel burn- as much as 20% less than current turboprop equivalents. Emissions will also be improved, as the European Clean Sky2 R&D partnerships yield further improvements in decarbonization.
This test flight also marks a first for the European Aviation Industry, being designed, produced, and completed entirely within the continent. Integrating assistance from GE Aviation Czech, Avio Aero of Italy and Poland, GE Aviation Advance Tech of Munich, and GE's Engineering Design Center of Warsaw. Local production lines also leverage extensive use of 3D printing. Freed of normal production constraints, engineers were able to distill 855 components of traditional manufacture down to a dozen printed parts. Perhaps most important for those customers tired of extensive regulatory paperwork, the engine is completely ITAR-free.
Continued development of the Catalyst continues through flight testing in the single engine Cessna Denali and the Beechcraft King Air with certification hopefully achieved in 2023.