Being Evaluated By The 418th Flight Test Squadron
Members of the 418th Flight Test Squadron are testing a new parachute canopy for the Advanced Concept Ejection Seat II. Testers are collecting data on the GR7000 parachute, which has been proposed to replace the current C-9 canopy used in the ACES II ejection seat. The testing is part of the Air Force’s ACES II Safety and Sustainability Improvement Program.
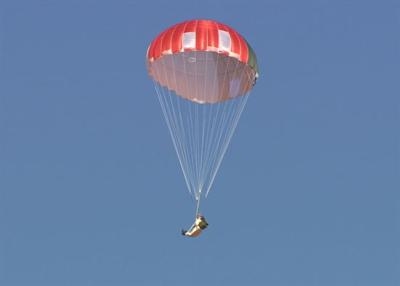
The ACES II ejection seat system has been used for almost 40 years and brought standardization to Air Force ejection seats in the A-10, F-15, F-16, F-22, B-1 and B-2. The standardization reduced cost and training time as maintainers and pilots only have to train on one type of seat.
“The overall test objective is to demonstrate the strength of the GR7000 parachute at worst-case ejection (situations), high-altitude mode 1 deployment and evaluate the steady-state descent characteristics of the GR7000 parachute,” said Alice White, 418th FLTS ACES II SSIP project manager.
White said since the initial fielding of ACES II in 1978, the Air Force has made two significant changes affecting ejection seat safety. The changes were unforeseen when ACES II was initially developed. The first change was expanding the allowable aircrew weight range -- originally 140-to-211 pounds -- to 103-to-245 pounds.
“Another significant change affecting the safety of the ACES II was the introduction of helmet-mounted devices, particularly the nuclear flash blindness goggles used by B-2A Spirit aircrew. The combination of larger allowable aircrew anthropometric range, and the added head-born weight of the helmet-mounted devices, increased the risk of having an unsafe ejection,” said Daniel Bush, 418th FLTS ACES II SSIP project flight test engineer.
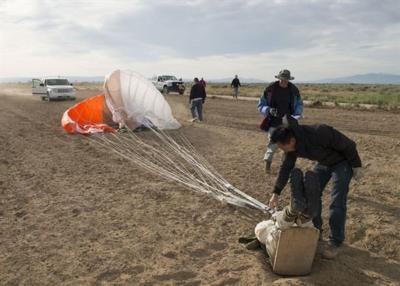
The GR7000 parachute is designed to handle the greater weight ranges for pilots and to provide a slower rate of descent and oscillation, according to the manufacturer.
In the past several weeks, testing of the GR7000 parachute consisted of 10 dummy drops, 20 live-person jumps and five drops using a crosswind deployment cylindrical test vehicle, which looks similar to an inert bomb. “Key performance values for this test are airspeed, altitude, rate of descent and canopy structural integrity. Riser loads and acceleration data also will be collected and analyzed,” said Dean Van Oosterhout, 418th FLTS ACES II SSIP project engineer.
For test purposes, the 418th FLTS contracted a Skyvan from Skydive Perris, out of Perris, California. Skyvans have been previously used for live jumps, dummy drops and airdrops. The plane has an anchor cable with a winch on the right side of the aircraft cargo hold and bench seats for parachutists and passengers running down both sides. According to the 418th FLTS ACES II SSIP project pilot, Maj. Duncan Reed, the Skyvan is able to meet test requirements to climb and level off between 16,000 and 17,000 feet median sea level and trim to between 90 and 100 knots-indicated airspeed, which is required for the cylindrical test vehicle drops.
The ACES II Safety and Sustainment Improvement Program has been on-going for many years, according to White. She said in the past year, a critical design review was held that culminated in the final seat design and a qualification effort ensued. “Approximately 80 percent of the qualification testing has been completed to date.”
Van Oosterhout said this particular testing of the GR7000 was for the B-2 version of the ACES II ejection seat, but data could be applied for all ACES II ejection seats currently using the C-9 canopy.
(Image provided with USAF news release)