Good News For Washington... Or Not
We screwed up? Well...
former Boeing 787 chief Mike Bair wasn't quite as blunt as that,
when he told Snohomish County, WA business leaders and politicians
this week the planemaker may reconsider its much-touted global
supply strategy, now causing headaches in the Dreamliner program...
but one could argue that was the underlying
implication.
Bair (right) -- ousted as 787 program manager two weeks ago, in
the aftermath of the announcement of a six-month delay following
months of assurances the aircraft's first flight and first delivery
remained on schedule -- kept a prearranged appointment to speak
Wednesday before the Snohomish County Economic Development Council
(EDC), reports the Seattle Times.
Now in a much-less visible role at Boeing,
Bair held the attention of the audience... particularly
when he spoke of a possible shift in Boeing's current philosophy of
outsourcing engineering and production of key aircraft components
to companies around the world.
Traditionally, Boeing performed the design and engineering work
for its airliners, and then contracted the build work out to
vendors, who would use Boeing blueprints -- a system known as
"build-to-print." The planemaker tried a new tact with the 787 --
it allowed vendors to handle the engineering work, too.
That business model hasn't paid great dividends for the 787, as
supplier trouble is the most commonly-cited reason for the
Dreamliner delay.
"Some of these guys we won't use again," Bair said bluntly,
referencing problem suppliers. "Some of them proved incapable of
doing it." In an interview with the Times following his speech,
Bair was even more candid -- expressing wonderment how some
suppliers seemed "unwilling, for whatever reason" to do the job
they promised.
"They just didn't do what we thought they could do," Bair said.
"Who knows why?"
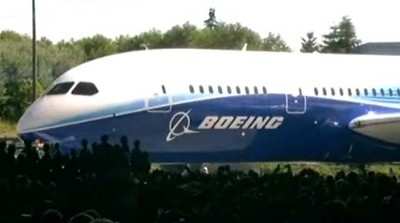
For the planemaker's next major project -- believed to be the
so-called Y3, a replacement for the erstwhile 737 narrowbody --
Bair said Boeing may opt for a new plan.
"The right way to do this would be to have all those big parts
across the street so you could just roll them in" to a single
manufacturing site, Bair said. "We'll see on the next airplane
programs whether we can accomplish something like that."
County leaders loved hearing that. The greater Seattle area
hosts three Boeing aircraft production plants, so the natural
assumption was Washington state would host such a "super-site,"
too.
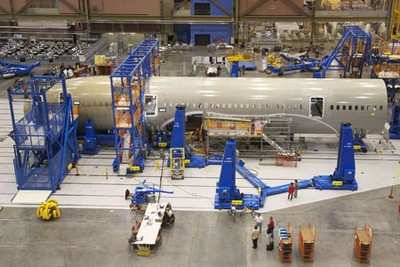
Well, you know what they say about "assume"-ing something. In a
later interview, Bair said the plant could be located in
Washington, "or someplace else. It doesn't necessarily have to be
here."
Boeing executives have a history of speaking boldly before the
EDC. It was here in 2003 -- as the state fought to win the
production site for the 787 -- then-Commercial Airplanes CEO Alan
Mulally summed up Washington's economic competitiveness with two
little words: "We suck."
The state legislature responded then, passing massive tax
incentives for Boeing to locate Dreamliner production in Everett.
Bair's comments set the stage for another showdown.
EDC President Deborah Knutson told the Times she already knew
Snohomish County didn't have a lock on winning Boeing's next major
commercial airliner. "I cannot imagine that the 737 replacement
will automatically come here," Knutson said. "From everything I've
heard, we'll need to work for it."
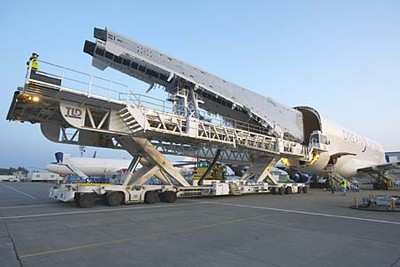
As for the 787, Boeing will have to work for it, too... to get
the plane out the door, and into the hands of several hundred eager
customers. Bair -- now head of business strategy and marketing for
Boeing Commercial Airplanes -- outlined the difficulties with the
knowledge of an insider, blessed with 20/20 hindsight.
Bair admitted problems with supplier parts for the first
aircraft overwhelmed the production system in Everett. The plant
was called on to pinch-hit on several areas -- either correcting
defects with supplier assemblies, or handling the engineering and
design work outright -- with somewhat predictable results.
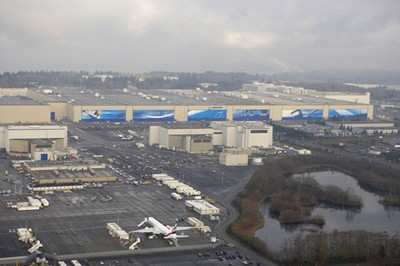
"That whole production system is built for 1,200 pieces," Bair
said. "Everything about it was designed for 1,200 parts. We threw
30,000 at it."