Mon, Jun 18, 2018
Validates 3-D Printing Techniques, According To Aerojet Rocketdyne
Aerojet Rocketdyne recently achieved a significant milestone by successfully completing a series of hot-fire tests of an advanced, next-generation RL10 engine thrust chamber design that was built almost entirely using additive manufacturing; commonly known as 3-D printing.
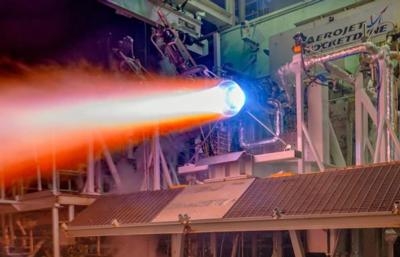
“This recent series of hot-fire tests conducted under our RL10C-X development program demonstrated the large-scale additive manufacturing capability we are maturing to help reduce the cost of this legendary engine system while continuing to provide reliable performance,” said Aerojet Rocketdyne CEO and President Eileen Drake. “This marks another important milestone in our effort to fully qualify components built with additive manufacturing for use in many of our production engine systems.”
The company first demonstrated that a 3-D printed copper alloy thrust chamber and nickel alloy main injector were possible just over a year ago when it completed successful testing of a 3-D printed thrust chamber assembly. The recent round of tests, which took place at the company’s facility in West Palm Beach, Florida, built on the prior work by incorporating a new 3-D printed copper alloy thrust chamber assembly design to accommodate a new re-generatively cooled nozzle that was 3-D printed from a nickel-based alloy.
Current production versions of the RL10 use a complex array of drawn, stainless steel tubes that are brazed together to form a thrust chamber. Incorporating 3-D printing into the process will reduce overall lead time by several months, which in turn will reduce production costs.
“Hot-fire testing helps us validate the approaches we are using to fabricate and join parts that are produced through additive manufacturing to ensure they meet our requirements for materials characterization, structural integrity and durability,” said RL10 Senior Program Director Christine Cooley. “We are also able to accurately define the amount of heat-transfer that is taking place so we can optimize the performance of our next generation of RL10 engines.”
“We continue to look for ways to insert additive manufacturing into our liquid rocket engine designs to not only reduce their cost, but to open up creative design spaces that the additive manufacturing process enables,” added Drake. “This latest round of testing demonstrates that we can systematically print and assemble an engine that can replicate the proven RL10 performance in a fraction of the time and at a reduced cost. Additive manufacturing technology also enables new approaches to engine design that we are now exploring through sub-system testing and validation.”
(Image provided with Aerojet Rocketdyne news release)
More News
Also: Vertical Flight Society, NBAA Maintenance Conference, GA Honored, AMT Scholarship For the first time, students from Embry-Riddle’s Daytona Beach, Florida, campus took t>[...]
Hazardous Weather Information Summary of significant meteorological information (SIGMET/WS), convective significant meteorological information (convective SIGMET/WST), urgent pilot>[...]
"The need for innovation at speed and scale is greater than ever. The X-62A VISTA is a crucial platform in our efforts to develop, test and integrate AI, as well as to establish AI>[...]
(FAA) Inspector Observed That Both Fuel Tanks Were Intact And That Only A Minimal Amount Of Fuel Remained In Each Analysis: According to the pilot, approximately 8 miles from the d>[...]
“Pyka’s Pelican Cargo is unlike any other UAS solution on the market for contested logistics. We assessed a number of leading capabilities and concluded that the Pelica>[...]