Thu, Mar 15, 2012
Will Assist In Development Of Full-Scale SLS Motors
A sub-scale solid rocket motor designed to mimic NASA's Space Launch System, or SLS, booster design successfully was tested Wednesday by engineers at NASA's Marshall Space Flight Center in Huntsville, AL. The 20-second firing tested new insulation materials on the 24-inch-diameter, 109-inch-long motor. The motor is a scaled down, low-cost replica of the solid rocket motors that will boost SLS off the launch pad.
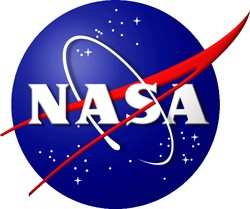
The test will help engineers develop and evaluate analytical models and skills to assess future full-scale SLS solid rocket motor tests. The next full-scale test, Qualification Motor-1 (QM-1), is targeted for spring 2013. Two five-segment solid rocket motors, the world's largest at 154-foot-long and 12-foot diameter, will be used in the first two 70-metric-ton capability flights of SLS. Previous ground tests of the motors included carbon insulation to protect the rocket's nozzle from the harsh environment and 5000-degree temperatures to which it is exposed. QM-1 will include a new insulation material, provided by a new vendor, to line the motor's nozzle.
"Test firing small motors at Marshall provides a quick, affordable and effective way to evaluate the new nozzle liner's performance," said Scott Ringel, an engineer at Marshall and the design lead for this test. "We have sophisticated analytic and computer modeling tools that tell us whether the new nozzle insulation will perform well, but nothing gives us better confidence than a hot-fire test."
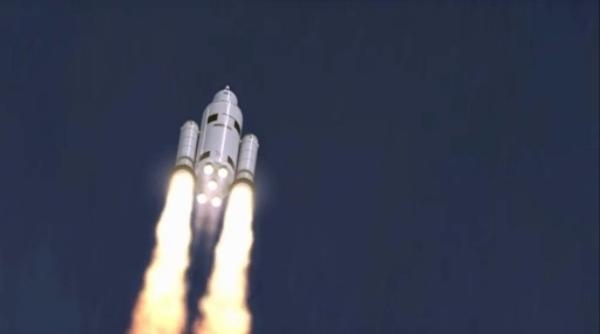
The test also includes several secondary objectives. The team introduced an intentional defect in the propellant with a tool designed to create a specific flaw size. By measuring the temperature inside the motor at the flaw location, the team hopes to gain a better understanding for the propellant's margin for error. Test data also will help the team better understand acoustics and vibrations resulting from the rocket motor's plume. In addition, NASA's Engineering and Safety Center will use test data to measure a solid rocket motor's plume and how it reacts to certain materials.
More News
Takeoff Roll The process whereby an aircraft is aligned with the runway centerline and the aircraft is moving with the intent to take off. For helicopters, this pertains to the act>[...]
“We’re proud of the hard work that went into receiving this validation, and it will be a welcome relief to our customers in the European Union. We couldn’t be mor>[...]
"Aircraft Spruce is pleased to announce the acquisition of the parts distribution operations of Wag-Aero. Wag-Aero was founded in the 1960’s by Dick and Bobbie Wagner in the >[...]
IDENT Feature The special feature in the Air Traffic Control Radar Beacon System (ATCRBS) equipment. It is used to immediately distinguish one displayed beacon target from other be>[...]
Aero Linx: Pararescue Air Force Pararescuemen, also known as PJs, are the only DoD elite combat forces specifically organized, trained, equipped, and postured to conduct full spect>[...]