Now, How About the Latest-Design Aero-Engine to Fly?
Just last weekend, the newest aero-engine in the world,
the DeltaHawk Diesel, flew. We
were able to corral the Project Engineer and Test Pilot, Doug
Doers, who also built both test aircraft -- a pair of Velocity
RGs.
First, it's good to know how a
program of this size gets started; it's not profitable, you know,
to make just one engine...
Doug told us, "A friend and fellow military guy, JP Brooks, came
to me years ago and wanted to build a Velocity and do some record
runs, like from Kadena (in Japan) to Texas. He wanted to know what
could be done. I'm an engineer -- although, until then at least,
not an engine designer -- and I told him that, for what he wanted
to do, what he'd need. The airplane? A Velocity can handle well
over max gross -- it's been done. They've flown at 3600 pounds and
up. It could hold the fuel."
He started by looking for an
automotive-based engine, as that was the only thing that had
anywhere near the specific fuel consumption he needed. He bought an
auto-conversion engine, but never received it. Doug said, "He
didn't get it -- it was one of those 'carbon-case' engines, that
never happened. That engine got sold a number of times..." It was
time for 'Plan B,' and a more-promising engine was on the radar
screen. "Continental had an engine in the works -- a four-cylinder,
Voyager-style water-cooled engine," Doug said, "but they
discontinued it, so we had an airframe that had no engine."
Plan C?
Doug continued, "So, he found a diesel -- a two-cycle,
turbocharged diesel sounded like the right way to go. They spent 18
months doing it, but never got the horsepower. Finally, JP told me,
'build me an engine.'" That sounded straightforward. "I come from
Milwaukee -- there's a lot of diesel experience there," Doug told
us. "In February 1996, we incorporated, and started an engine
company."
He skipped a step or two, and
said, "Three million dollars later, we have our tenth engine, and
it's flying."
There's more to flying than flying, though, and Doers,
"...started delivering some (non-flying) engines. We're going into
an extensive test program. Here in Racine (WI), we're running a
test stand, a dyno, and a test aircraft. (The dyno isn't the best
way to test an engine, in a lot of ways.)" Another engine went
East, to be hooked up to space-age telemetry. "There is a company
in Virginia (CTSI) that's running a test program there, too," Doug
explained. "Most of the employees also work for NASA, or did at one
time. They can look at cylinder pressure of all 4 cylinders
simultaneously -- they have plenty of computers. They think they
can predict failure by mapping vibration. They think they can
determine what's a normal signature, and what's not. We get testing
on our engine. We're letting them try." The testing will be quite
welcome. "We want to keep that engine ahead of our airplane
engine," Mr Doers said, "and our airplane engine ahead of our
customers'. We don't know of any problems, yet -- but we're trying
to find them."
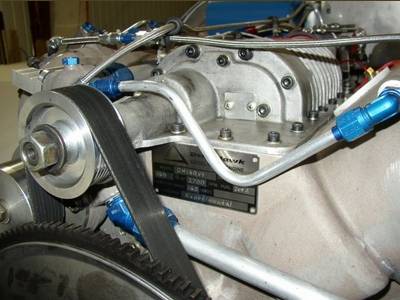
In general:
The engine is aluminum, water-cooled, and just one cubic inch
larger (at 202 ci, or 3.3 liters) than the Wrights' engine of a
hundred years earlier; but the similarities pretty much end there.
The DeltaHawk is a supercharged and turbocharged V-4 two-stroke
diesel. (The supercharger is there to aid in scavenging, and for
starting; the turbo, which should keep the rated horsepower to over
12,000 feet, is significant at engine speeds as low as 600rpm, and
is 'on the pipe,' starting around 1500.) Doug said that an
in-flight failure of the supercharger was simulated, and it was no
big deal: "We have lost a belt on the supercharger, and it keeps
running on the turbocharger." The alternator annunciator was a good
clue (they run off the same belt); but there was no power loss. He
noted, "In flight test, when we de-spool the turbo, we've noticed
that we could still get a significant boost from ram-air, that
indicated that we might still have decent airflow, even if the
turbo spooled down.
"We have a long way to go on that,
testing, before we would say it'll do that." Important, if you have
the rare pleasure of losing a supercharger (right, on top), and
follow that by dropping rpm to idle for landing -- and need to go
around. Doers noted, "If the turbo is the only [air] pump on the
engine still working, you'll still be OK in the air; just plan for
no go-around. You might be lucky -- you probably would -- but don't
test it, then." Good advice, for any situation.
Power?
"We call it 160 hp," Doug says, and it should deliver at least
that, "...to 12,000 feet+." [It runs over 180 in the test cell;
"with an intercooler, it'll run over 200," Doug says.] It weighs
about the same as an IO-360-200, right at 327 pounds, counting the
exhaust system and turbo; the intercooler would add eight pounds to
that total. There's always something nice about turbos: "In flight,
we have more power with the '160' at 5000 feet, than the 360-200,"
he said; "and it's really quiet, too."
It typically turns a little lower rpm than its gasoline-powered
performance partner, so prop tip speeds can be reduced, as well.
"We have two Velocities, one with a Lycoming IO-360A2B, and the
DH-160. We turn 2240 with the gas engine, 2170 with the diesel."
The power curves of the two engines are different, with the
diesel's peak torque delivered at lower rpm. "We have a number of
prop companies that are working with us," Doug reassured us. "We
have a constant-speed capability, too, in case anyone wants to do
that." Even so, Doug predicts that with the present prop, "We'll be
able to redline it (2700 rpm) at 7000 feet."
Installation:
The DeltaHawk is not unusual in its
space and mounting requirements; but it is turbocharged and
water-cooled; and one model is intercooled, so additional
consideration may be required in cowling design. It's a diesel,
too, and even though they recommend Jet-A, Doug says, "We run a
[fuel-] warming loop in our fuel, and we recommend users to do the
same."
Performance:
The DeltaHawk is a real fuel miser. The first flight consisted
of one takeoff and landing, including about 38 minutes in the air,
cruise at just 140 knots (the chase plane was max'd out), and a 130
knot climb at full throttle, at 1000+ fpm ("I was watching other
things," Doug said.) Additional time (warm-up and taxi) added 21
minutes of mostly idling. The test flight burned 2.5 gallons. "We
weren't running high power levels, except during takeoff and
initial climb, and maybe 20 seconds at full power, climbing."
See it at Oshkosh.
DeltaHawk has had a booth at OSH since 1996, "...when we came
with a flywheel and crank. In 1998, we taxied. This year, we intend
to have it in the pattern -- we've got to get our 40-hour, and
several teardowns, done. I think we'll make it, for the flyovers,"
Doug said.
Price and availability:
It's been a long time coming, but with that first flight behind
them, and with over a dozen engines in test and development,
DeltaHawk has established some initial pricing. For the basic 160,
you'll pay $20,000; the 200 hp is currently $24,000; and there is a
160hp vertical-shaft variant for $21,000. Those prices are expected
to go up, right at Oshkosh time. Starter and alternator are
included, along with the turbo, oil and water pumps, piping to the
turbo, all engine-specific tubing and pipes; but it does not
include installation-dependent parts such as radiators, heat
exchangers, exhausts, etc. Doug said, "We hope that by this time
next year we'll be delivering to the sport aircraft community."
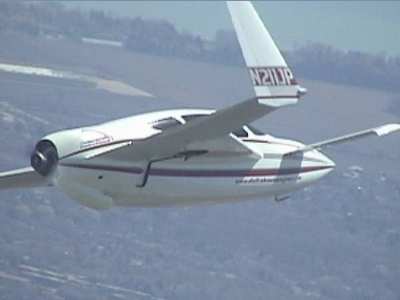
Shortly thereafter, we'll be on the lookout for an over-gross
Velocity to lift off from Japan, heading for Texas...
[...and thanks to Rip Edmundson, who took the exclusive closeups
for ANN, on Thursday afternoon!]