Company Responsibly Addresses Flawed Components
Van’s Aircraft, the famed light-sport aircraft marque and maker of the perennially popular RV6/6A, RV7/7A, and numerous additional kit aircraft models, has published new and updated documents for customers in possession of aircraft kits comprising laser-cut parts. The described customers, on Tuesday, 03 October 2023, were to have received an email containing a link to a newly-established web portal via which they may select requested replacement parts.
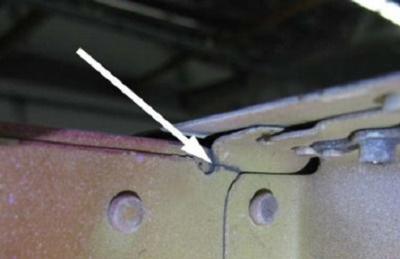
Van’s has also made available to its customers a series of online documents including a new engineering assessment report the company encourages its customers to read in full. Subject report describes the work Van’s have done and the results of testing and assessment performed by the company’s engineering team and a contracted third-party testing company. All laser-cut parts have been classified either as “Recommended for Replacement” or “Acceptable for Use.” Those parts classified as Acceptable for Use are functionally equivalent to punched parts and may be used in an aircraft. Any parts classified as Recommended for Replacement should be replaced or addressed as discussed in the engineering assessment document.
The status of each part is displayed in the updated Laser-Cut Parts List document, as well as the new web portal’s parts list.
A detailed review of documentation included with kits shipped to customers revealed upwards of one-thousand instances in which Van’s erroneously informed customers their kits might contain laser-cut parts. In fact, the kits in question did not contain laser-cut parts. Customers in receipt of inaccurate data pertaining to their kits will be contacted by Van’s regarding the status change of their kits.
The updated Van’s documents may be viewed in their entirety at:
- Engineering Assessment document (new, PDF): www.vansaircraft.com/wp-content/uploads/2023/09/Laser-Cut-Parts-Engineering-Evaluation-R11.3.pdf
- Laser Cut Parts List document (updated, PDF): www.vansaircraft.com/wp-content/uploads/2023/09/Laser-Cut-Part-List-Revised_R5.6.pdf
- Parts Identification Guide (PDF): www.vansaircraft.com/wp-content/uploads/2023/08/Laser-Cut-and-Punched-Part-Identification-Key-with-edits.pdf
Information selected by customers on the aforementioned web portal will inform Van’s future production-planning needs. Van’s will update delivery timelines and other parts-related information, and communicate such to customers over time.
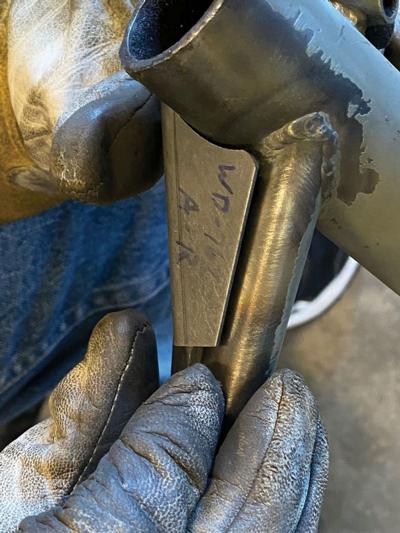
Van’s respectfully reminds customers the prevailing situation is costly, time-consuming, and will take the company some time to work through. Van’s states: “We certainly also understand that this situation is time-consuming and inconvenient for our builders. To sustain the company, Van’s must produce and ship new kits and parts while simultaneously producing and shipping replacement parts. The amount of work and time involved in resolving this issue will depend greatly on how our customers adopt and implement the classifications and recommendations documented in the Van’s engineering assessment document, simply because the number of parts requested by customers will primarily define the actual production volume and timelines for those parts.”
In early 2022, Van’s Aircraft commenced subcontracting the manufacture of select aircraft parts to fabrication concerns utilizing laser cutting processes.
The decision to subcontract parts manufacturing was, according to Van’s: “ … made after completing a formal manufacturing process evaluation and extensive fatigue testing of materials used in the manufacturing process, with the purpose of increasing the production capacity for some parts during a period of high demand.”
Between February and June 2022, a significant number of Van’s customers reported cracks having formed in parts with laser-cut holes. The company immediately undertook corrective action, conducting testing of cracked parts, assessing the nature of the defects, and devising corrective measures germane to such.
Van’s determined the parts of greatest concern to be:
- Vertical stabilizer, rudder, and elevator spars on all RV-7, RV-8, RV-9, RV-10, and RV-14 empennage/tail kits.
- Horizontal stabilizer spars in RV-7/8 empennage kits.
- Flap and aileron spars shipped early in the laser-cutting process, in RV-7, RV-8, RV-9, RV-10, and RV-14 kits.
Seeking to safeguard its customers and the larger aviation community, Van’s, on 04 July 2023, stated on its website: “We encourage people to pause building of the above specific kits that include laser-cut empennage/tail, aileron, and flap-spar parts. We will be replacing these components and providing further guidance. Even though testing of these specific parts is not yet complete, Van’s is erring on the side of caution by identifying those parts now and will recommend the replacement of these parts due to the relatively high loads carried by those specific parts. We will communicate directly with all affected customers concerning these parts via email this week, to inform those customers as to what steps should be taken. We are executing an initial run of replacement parts on our punch presses now and will be making additional production runs.”
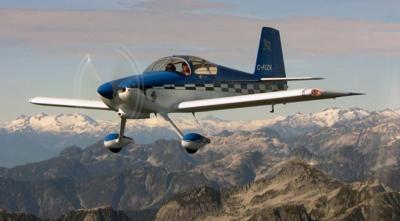
The statement continued: “Our testing program for this issue is ongoing and focused on reviewing the various hole diameters and material thicknesses/types that were used to produce the laser-cut parts. These variables, as well as variations in manufacturing process parameters, can result in a marked difference in the potential for a crack to form in a given hole. We will prioritize testing and manufacturing of replacement parts based on these differences. We are also reviewing the metallurgy of the holes at the third-party test lab, in order to better understand the origin and cause of the observed cracks. From that, we will gain a greater understanding about these cracks and at what stages in the process they are formed (when cut, when dimpled, when riveted). We expect to receive those results soon, even before the full spectrum of overall testing is completed, and we will communicate that information when available.”