National Full-Scale Aerodynamics Complex (NFAC) Is Home To Two Such Test Facilities
They are considered indispensable. Those at the National Full-Scale Aerodynamics Complex (NFAC) at Moffett Field in Mountain View, California, who observe their contributions every day agree the craftsmen employed there are not only integral to the work at NFAC but play a vital role the Arnold Engineering Development Complex (AEDC) mission as a whole.
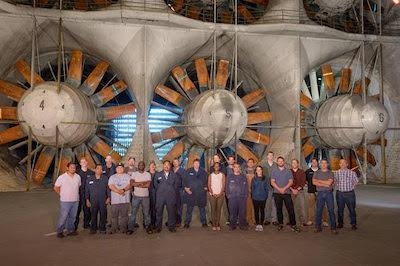
“They are essential,” said NFAC Branch Manager Jeff Johnson. “We couldn’t perform this mission without them.”
The craft crews at NFAC are not only responsible for performing all the maintenance around the facility, they are also charged with the installation of test articles in each of the two large wind tunnels at NFAC and the operation of the tunnels themselves.
There are currently 16 craftsmen employed at NFAC. They are broken up into three different groups – mechanics, electricians and instrumentation technicians. Within the mechanics is a subgroup of employees who possess aircraft maintenance experience and certification, which allows these aircraft mechanics to work more extensively on engines, rotorcraft and aircraft models that are tested in the NFAC wind tunnels.
NFAC is home to the two largest wind tunnels in the world – a 40- by 80-foot wind tunnel circuit and the 80- by -120-foot test section. The facility is used to conduct aerodynamic testing on a wide range of full- and large-scale test articles, including airplanes, helicopters, tiltrotors, tractor trailers, parachutes, planetary decelerators, wind turbines and more. “Because of the uniqueness of our facility, every test is different, so it requires our team to be flexible and creative in how we get these test articles installed and set up,” Johnson said. “There’s always something unique and challenging associated with the type of test work that we do here at the NFAC, so our craft crew has to be pretty creative, and they do a really good job of that. They excel at thinking outside the box and coming up with clever ideas to get test articles installed and get the facility operational.”
The craftsmen at NFAC handle the installation and setup of test articles. Because large items are tested in the facility, crew members must often utilize the large overhead cranes to install the articles in the test sections. Johnson said members of the craft crew are certified riggers and crane operators.
Once a test model has been installed in a wind tunnel, the craftsmen complete the installation and hookup of electrical connections, sensor cabling and other model utilities prior to the test. Most NFAC tests require custom sensor cabling to transmit sensor data or control commands to and from the model into the data acquisition system or model control console.
Johnson said NFAC technicians are extremely talented at fabricating custom wiring harnesses for very demanding applications. “Because of the size of our models, the installation of the model into the tunnel is a pretty involved process,” he said. “It takes a lot of planning and teamwork but, ultimately, the execution is done by our craft mechanics and technicians.”
Before being allowed to serve as tunnel operators, the craftsmen must undergo a certification process requiring a significant amount of on-the-job training. “It takes a lot of experience to safely run this big wind tunnel,” Johnson said.
Among the craftsmen’s recent successes is the NASA/Army Tiltrotor Test Rig. The TTR is a new test capability developed to study advanced tiltrotors and develop databases for design code validation. NFAC crew members have been involved in the multiyear development of TTR in preparation for the first test in NFAC.
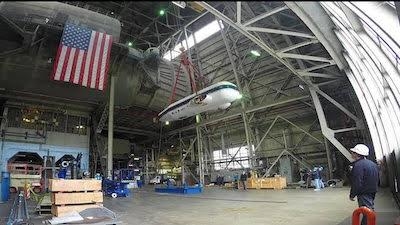
Crew members were involved in the installation of the TTR, as well as the installation of a three-bladed fully-controllable proprotor measuring 26 feet in diameter. “This installation of the TTR was the first wind tunnel test of this new capability,” Johnson said. “We were able to successfully demonstrate the operational capability of the rig and achieve the highest speed ever obtained in the wind tunnel in forward flight for a tiltrotor of this size. So it was quite an accomplishment by our team.”
The NFAC craftsmen also played a significant role in bringing the facility back online following a June 2017 incident in which a collapsed wall panel damaged one of the six large fan motors that powers the NFAC wind tunnels. “Our craft crew was highly involved in getting us back online,” Johnson said.
Each of the six fans measures 40 feet in diameter and contains 15 large wood-laminated blades. Each fan blade is 12 feet long and weighs more than 800 pounds. All 15 blades in one of the fan motors were damaged as a result of the collapsed panel.
Because it will potentially take years to have new blades fabricated, personnel at NFAC decided to “borrow” blades from the other fan motors to replace the damaged blades, Johnson said. Three blades were pulled from each of the five “healthy” fan motors, and 12 were placed in the damaged motor. The three additional blades were placed into storage. “That was a very extensive process because these blades are so heavy, delicate and require careful handling,” Johnson said. “The crew had to use a special hydraulic cart system to clamp onto the blade, unbolt it, lower it and tilt it from vertical into a horizontal position, and then transport it to the lower level because the six fan motors are arranged in two rows of three. We took blades out of the upper three fan motors, installed a winch system to lower them carefully down to the ground and then transferred them to the damaged fan motor and reinstalled them.
“That whole exercise was pretty involved and hazardous. The engineers and craft workers got together to identify the potential hazards and develop a safe plan. It was a big job, and the craft crew worked painstakingly over several months to safely move all those blades from the other fans and get us operational again.”
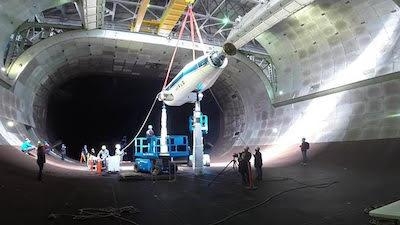
Johnson said reducing the number of blades from 15 per fan to 12 has had a surprisingly small impact on the speeds at which NFAC can operate. He added the facility will likely continue to operate in this manner until new blades are designed and fabricated.
Following the incident, the NFAC craftsmen worked alongside NASA welders and craftsmen sent from Arnold Air Force Base to repair damage to the fan shroud. Another difficult task that the craft team members contributed to was repairing the damaged stators, which are the stationary blades behind the fans that help direct the airflow and remove swirl. These damaged stators had to be removed for refurbishment and then reinstalled.
Along with completing the cleanup of the facility, the NFAC craftsmen also helped assess the health of the drive shaft and hub that supported the blades on the damaged fan motor.
“The craft helped considerably with evaluation of the bearings that support the drive shaft and also checking electrical systems out to make sure that when we first spun it up again it was going to be safe to operate,” Johnson said.
NFAC personnel completed an inspection of the interior of the tunnel circuit afterward to ensure the liner of the circuit was secure and that no further issues would arise. “We had to do a complete, thorough inspection of the tunnel circuit and, in the process, the mechanics found several other places where some panels were loose and fasteners were in need of repair,” Johnson said.
These repairs have since been completed, and the NFAC 40- by 80-foot test section has been back online for a little over a year. The 80- by 120-foot section is undergoing repairs and should be back online in February 2020. “In addition to all the post-mishap refurbishment work and ongoing test support, the craft crew also must fit in an extensive amount of facility maintenance work,” Johnson said. “We have a very lean crew, and it is a constant effort to schedule all the preventative maintenance work that is needed to sustain the capability. The craft team is extremely agile and is outstanding at adapting to the dynamic work environment associated with operating a unique wind tunnel complex.”
Johnson said whatever the task, the NFAC craftsmen pull together and work cooperatively to accomplish it. “If somebody needs help, they’re willing to jump in and do whatever it takes to get the job done,” he said. “We could not meet our mission without them.”
(Images provided with USAF news release)