That Guy In "The Graduate" Was Right
Even 40 years after his father's friend whispered what he saw as
the future ("Plastics!")into Dustin Hoffman's ear in "The
Graduate", it turns out he was right -- and then some,
particularly for the aviation industry.
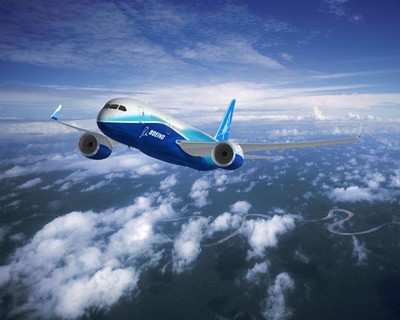
Aluminum components that were once the norm for aircraft
manufacturing are taking a back seat, in many cases, to their
lighter-weight, plastic-based composite cousins, reports the New
York Times.
All of this, of course, is to meet the highly-competitive demand
from airlines, which are reacting to public pressure to replace
their older aircraft with more fuel-efficient, reduced-emissions
craft that are lighter-weight and less polluting.
Utilizing plastic-based components can significantly reduce
weight in an aircraft. And of course they are already in use in the
automobile industry, sporting goods manufacturers, and others who
have seen the financial benefits from this new use of plastics.
In order to be part of the competition, aircraft and component
manufacturers are scurrying to meet airline needs with new designs
that make more use of these composite materials.
What Is A Composite?
A composite may be thought of in terms of the output of two
individuals working together being superior to those individuals
working separately. Does that metaphor not work for you? Okay, a
composite is a combination of two or more industrial materials that
exhibits the best properties of each and additional qualities that
the individual materials do not possess alone.
In the industry of aerospace, composites are made of nonmetallic
fibers, such as carbon, fiberglass or aramid, that are embedded in
a resin of plastic or epoxy molded and then cured in autoclaves at
high temperatures.
A composite material like carbon fiber -- stronger and stiffer
than aluminum, titanium or even steel -- has a relative
weight/volume that is half that of aluminum and one-fifth the
weight of steel.
How Is It Being Used?
Both Boeing and Airbus plan to use composites in at least half
the structural components of their latest wide-body jets, the 787
Dreamliner and the A350-XWB.
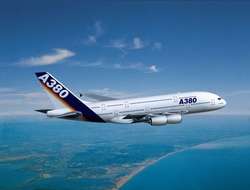
The 787 is being built using an all-composite fuselage and wing,
and according to Boeing, will burn about 20 percent less fuel than
similarly-sized jets.
Airbus' 555-seat A380 superjumbo is made of 25 percent composite
and other advanced materials, offering a weight saving of about 15
metric tons.
It was back in the 1960s that Boeing began experimenting with
fiberglass with its 747 program, using it on certain control
surfaces of the plane, as well as on fairings and trailing edge
panels on the wings and tail.
Boeing's use of ultra-light materials has increased
significantly over the past decade, with the 777 wide-body made of
about 11 percent composites, most of it in the tail section.
Airbus has also has boosted its use of composites in the wing
and tail sections of its single-aisle A320 family, as well as in
its widebody A330 and A340 jets.
Its A350 will be made of 52 percent composites and achieve
comparable levels of fuel efficiency as Boeing's 787.
"The trend is clearly towards more composite," Jeff Turner, the
chief executive of Spirit Aerosystems, which builds carbon-fiber
and other composite components for Boeing and Airbus. "Whether it
totally eclipses the metal airplane or not, I couldn't say."
Much of the companies' future investments will be used for
finding uses for new, lighter materials to increase the fuel
efficiency of the planes.
And recent advances in composite technology could not come at a
better time for the airlines.
Saving On Fuel Costs, Maintenance
"The biggest thing about composites is that it gets fuel costs
down," said Howard Wheeldon, an aviation industry strategist at BGC
Partners in London.
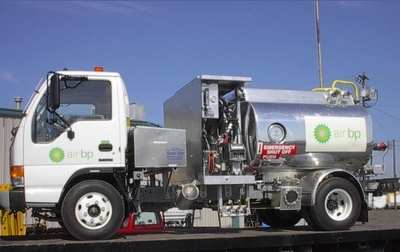
Because rising oil prices cut into airline profits, it is
forcing carriers to demand better performance and longer range from
its new planes.
According to IATA, although aircraft fuel efficiency has
increased about 2.5 percent a year since 2003 - saving the industry
$2 billion a year - the industry expects its fuel bill to rise to
$119 billion this year, up $8 billion from 2006, representing 26
percent of operating costs.
There is additional good news with lighter planes. Not only do
they burn less fuel, because airport landing fees are partly based
on the weight of the aircraft, a lighter fleet can represent a
significant cost saving to airlines.
According to IATA, airlines and passengers pay at least $43.5
billion a year in airport landing fees and other taxes, equivalent
to 11 percent of global airline revenue.
Manufacturers also note that composites resist fatigue and
erosion better than metal, which reduces maintenance costs because
regular jet inspections do not need to be as frequent or
extensive.
Maintenance intervals for composite-built jets could be as much
as twice as long as those for aluminum planes, said Jeanne Yu, an
engineer who heads Boeing's environmental performance group.
Regulators are likely to await proof of those claims, however,
before approving significant changes to current inspection
regimes.
According to the International Civil Aviation Organization,
airlines spent $41.7 billion on maintenance in 2005, equivalent to
10 percent of total industry operating costs.
Besides cutting fuel consumption, said Scott Hamilton, an
analyst based in Issequah, WA, "savings on maintenance is the main
factor that makes composites attractive to airlines."
Benefit To Manufacturers, Passengers
Composites also simplify
the production process for jet manufacturers because they allow for
the creation of larger, more integrated parts.
According to Boeing, this could eventually help accelerate its
assembly lines by as much as 40 percent.
Additionally, a lot of "waste" is eliminated because composite
sections are cast into precise molds; they do not, like aluminum,
have to be cut and shaped from sheets of bulk material.
And let's not forget the passenger, whom airlines are in the
business to serve. Composites make it possible for airlines to
significantly increase cabin air pressure because they are stronger
and stiffer than aluminum. That would mean less fatigue for
travelers on long-haul flights.
Cabin air pressure in aluminum wide-body jets is typically
equivalent to what a person would experience at an elevation of
8,000 feet, above sea level, a factor contributing to that
fatigue.
Additionally, composites' resistance to corrosion means that the
relative humidity of the air inside the cabin can be higher than
the 10 percent to 20 percent typicaly found on today's planes. This
decrease in dry air would be another improvement for passenger
comfort.
Although engineers may debate the merits of different
composite-designed jets, it is clear that aircraft manufacturing
has crossed a technological threshold with the 787 and the A350
that will shape on the way future aircraft are built.
"There is no going back," said Wheeldon of BGC Partners.
"Plastic has finally made its mark in the big toys."