Investigation Shows Longeron Was Outside Specs
An investigation into what led to the in-flight breakup of an
F-15C Eagle fighter in November 2007 uncovered structural beams in
several aircraft that weren't up to spec, US Air Force officials
said Thursday. Investigators also discovered one of the accident
aircraft's four cockpit longerons, which support the fuselage
during high-g maneuvers, was thinner that design specifications
called for.
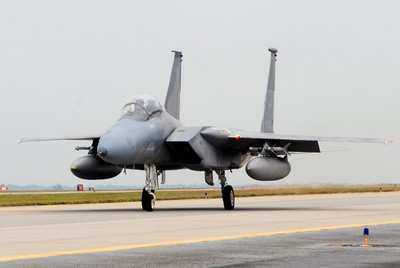
Colonel William Wignall, head of the USAF team that investigated
the accident, confirmed the upper right longeron on the Missouri
ANG aircraft had manufacturing defects. That longeron cracked apart
under the stress of a 7G turn, the colonel said, leading to the
other longerons failing as well, which then caused the cockpit to
separate from the rest of the fuselage.
The pilot was able to eject from the cockpit, but suffered a
broken arm when the canopy snapped off.
Subsequent inspections
of other F-15s throughout the USAF fleet have uncovered a wide
range of issues with other longerons -- including those that are
too thin, or have surface imperfections that may place too much
stress on the structure. The flaws on some beams are relatively
minor; others have larger problems, reports The Los Angeles
Times.
Nine other F-15s have been found to have cracks in their
longerons, similar to those found on the accident aircraft.
The incident led to the grounding of the Air Force's F-15 fleet.
As of January 9, the Air Force approved 60 percent of F-15 A
through D models to return to service with no flight restrictions,
though inspections continue on other planes. Problems have been
found on F-15s built between 1979 and 1985.
Air Force officials want answers on how, and why, apparently
substandard structural parts were used to build what at the time
was the USAF's front-line fighter aircraft. Trouble is, it's hard
to say where the process broke down.
No one source of the problem can be isolated, said General John
D.W. Corley, the commander of Air Combat Command. "This isn't just
about one pilot in one aircraft with one bad part," Corley said. "I
have a fleet that is 100 percent fatigued, and 40 percent of that
has bad parts. The long-term future of the F-15 is in question.
"Don't lose sight of the fact this is not just a bad part, it is
a bad part that has been under stress for 25, 26, 27 years," Corley
added. "It is the interaction between the fatigue, stress and that
part that causes the crack."
The F-15C involved in the November 2 accident was manufactured
in 1980, by McDonnell Douglas. Boeing purchased that planemaker in
1997, and assumed production of the Eagle at that time. It's
unclear whether Boeing will be held liable for the structural
problems.
"We've had great involvement from Boeing during the
investigation," Wignall said. "In fact, they're the ones who
determined the longeron was the problem. This was then confirmed by
the Air Force Research Laboratory."
A Boeing spokeswoman wouldn't comment on the findings, saying
the company is awaiting word on the roughly 180 F-15s that remain
grounded. As ANN reported earlier this
week, those aircraft may be grounded permanently.
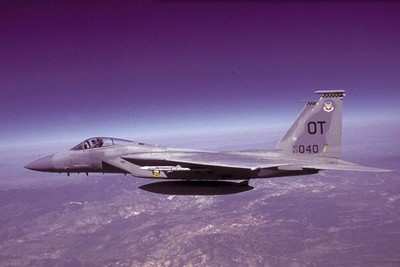
The F-15 was originally life-limited to 4,000 flight hours when
it entered service in the mid-1970s. Subsequent testing by
McDonnell Douglas validated the aircraft could safely fly for twice
that time, and the limit was raised to 8,000 hours. The accident
F-15C had 6,000 flight hours, according to the Times.
The newest F-15, the -E Strike Eagle, is life-limited to 16,000
flight hours.