Tue, Apr 21, 2015
FAA Certified The Part In February
The GE90 engine, which was the first jet engine to utilize composite fiber polymeric material on the front fan blades 20 years ago, achieved another milestone ... becoming the first GE engine to incorporate an additive manufactured component for the housing on the T25 sensor.
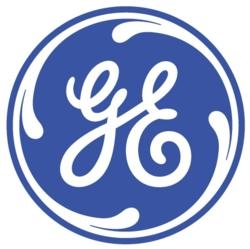
The FAA granted certification of the T25 engine sensor for the GE90-94B engine in February. The upgraded T25 sensor, located in the inlet to the high pressure compressor, is being retrofitted into more than 400 GE90-94B engines in service. The T25 sensor provides pressure and temperature measurements for the engine’s control system.
“Additive manufacturing has allowed GE engineers to quickly change the geometry through rapid prototyping and producing production parts, saving months of traditional cycle time for the T25 sensor housing without impacting the sensor’s capabilities,” said Bill Millhaem, general manager of the GE90/GE9X engine program at GE Aviation.
The T25 sensor housing is just the start of additive manufacturing at GE Aviation. Several next-generation engines currently in development will incorporate the advance manufacturing technique. On the LEAP* engine for narrowbody aircraft and the GE9X for the Boeing 777X aircraft, GE Aviation will produce part of the fuel nozzles with additive manufacturing.
Additive manufacturing represents a significant technology breakthrough for GE and the aviation industry. Unlike traditional manufacturing methods that mill or cut away from a metal slab to produce a part, additive manufacturing (also called 3D printing) "grows" parts directly from a CAD file using layers of fine metal powder and an electron beam or laser. The result is complex, dense parts without the waste, manufactured in a fraction of the time it would take using other methods.
Additive manufacturing has many advantages. It allows GE to design parts with unique geometries that were impossible to create using traditional machining methods. These additive manufactured components can reduce part count by replacing assemblies with single parts and can be lighter than previous designs, saving weight and increasing an engine’s fuel efficiency.
More News
Pilot Also Reported That Due To A Fuel Leak, The Auxiliary Fuel Tanks Were Not Used On June 4, 2025, at 13:41 eastern daylight time, a Piper PA-23, N2109P, was substantially damage>[...]
Have A Story That NEEDS To Be Featured On Aero-News? Here’s How To Submit A Story To Our Team Some of the greatest new stories ANN has ever covered have been submitted by our>[...]
From 2023 (YouTube Edition): Reflections on War’s Collective Lessons and Cyclical Nature The exigencies of war ought be colorblind. Inane social-constructs the likes of racis>[...]
Aero Linx: Colorado Pilots Association (CPA) Colorado Pilots Association was incorporated as a Colorado Nonprofit Corporation in 1972. It is a statewide organization with over 700 >[...]
High Speed Taxiway A long radius taxiway designed and provided with lighting or marking to define the path of aircraft, traveling at high speed (up to 60 knots), from the runway ce>[...]