Sheds 2,700 Pounds -- On Paper
Engineers have removed more than 2,700 pounds of unwanted
estimated weight from the short-takeoff/vertical-landing (STOVL)
version of the F-35 Joint Strike Fighter, while increasing
propulsion efficiency and reducing drag. The result is an F-35 JSF
design recommendation that is expected to meet or exceed all of its
performance requirements.
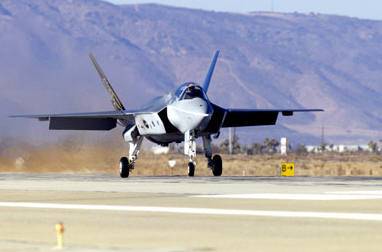
"The F-35 is now tracking ahead of its Key Performance
Parameters, and past concerns about the aircraft's aerodynamic
performance have diminished," said Tom Burbage, Lockheed Martin
executive vice president and general manager of F-35 JSF program
integration. "Because of the design similarities among the three
F-35 variants, many of the STOVL-version refinements will translate
to the conventional and carrier versions, which already met their
performance requirements even before the STOVL improvements were
instituted."
The F-35 team anticipates final approval of the STOVL revisions
when the US Defense Acquisition Board meets on Oct. 14.
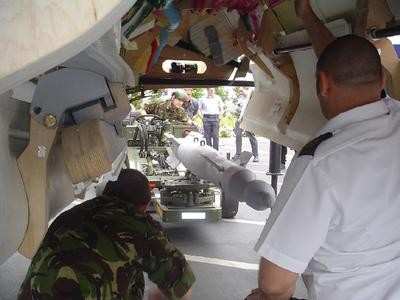
"We have addressed every known aspect affecting STOVL
aerodynamic performance and shipboard compatibility," said Rear
Adm. Steven Enewold, F-35 JSF program executive director. "We feel
our proposed configuration is operationally viable. The next step
is to get the trade-study results implemented into the detailed
STOVL design package."
With first flight expected in August 2006, production becomes
the program's central focus. All four of the first test aircraft's
major subassemblies are now in work. Last month BAE SYSTEMS began
assembling the aft fuselage and tails in Samlesbury, England, and
Lockheed Martin started wing assembly at the company's Fort Worth
plant. In May, Northrop Grumman kicked off F-35 assembly when it
began making the center fuselage in Palmdale (CA). Forward-fuselage
assembly started the following month in Fort Worth. Production of
control surfaces and edges will soon be under way at Lockheed
Martin's Palmdale site.
Final assembly of the F-35 is
planned to start next spring in Fort Worth, with completion of the
first aircraft anticipated in late 2005.
The program already is preparing for the challenge of operating,
supporting and sustaining thousands of F-35s worldwide. Nine
countries currently are engaged in the aircraft's development and
are expected to begin adding F-35s to their fleets early in the
next decade. Many other nations have expressed interest in the
aircraft, and the roster of international F-35 customers is likely
to grow. The task of sustaining such a large number of aircraft
over a geographically dispersed area for more than 40 years will be
made possible by the F-35's exceptional reliability, its
next-generation onboard diagnostics, its standardized and
simplified maintenance processes, streamlined supply-chain
management and many other advances over current fighters.
The F-35 is a next-generation, supersonic, multi-role stealth
aircraft designed to replace the AV-8B Harrier, A-10, F-16, F/A-18
Hornet and the United Kingdom's Harrier GR.7 and Sea Harrier.
Lockheed Martin and its principal industrial partners Northrop
Grumman and BAE SYSTEMS are employing an array of advanced and
highly accurate manufacturing machines to help the F-35 achieve its
goals of affordability, quality and assembly speed.
Three F-35 variants - a conventional takeoff and landing (CTOL),
a short-takeoff/vertical-landing (STOVL) and a carrier variant (CV)
- each derived from a common design will ensure that the F-35 meets
the performance needs of the US Air Force, Marine Corps, Navy, the
U.K. Royal Air Force and Royal Navy, and allied defense forces
worldwide, while staying within strict affordability targets.
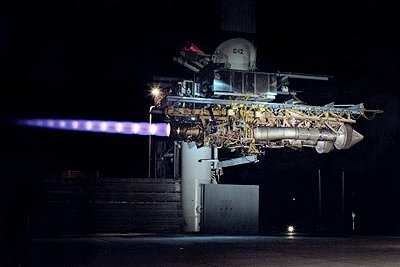
Lockheed Martin is developing the F-35 in conjunction with
Northrop Grumman and BAE SYSTEMS. Companies worldwide are
participating in the F-35's development. Two propulsion teams, led
by Pratt & Whitney and General Electric, are developing
separate interchangeable engines for the F-35.