Multiple Engine Options For The Aircraft Presented Unique Challenges
Industry and government engineers have mitigated an ongoing engine integration issue for the CH-53K King Stallion – the new heavy-lift helicopter from Sikorsky for the United States Marine Corps.
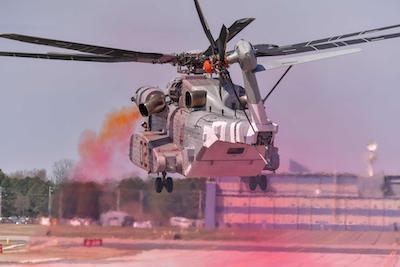
This “tiger team” of experts from a variety of engineering backgrounds came together to find and optimize aircraft modifications using state-of-the-art computational modeling methodologies, risk management, flight test data and Systems Engineering tools.
“Bringing together the tiger team exemplifies the importance and purpose of an integrated test team,” said Col. Jack Perrin, PMA-261 program manager, heavy lift helicopter program office. “It was great to see the team turn the corner for the program and produce a resolution to an ongoing problem. This was a priority for NAVAIR, industry and the Marine Corps, and the team hit it out of the park,” he said.
The program office oversees both the CH-53E Super Stallion, which is currently in use by the Marine Corps, as well as the new CH-53K.
The CH-53K King Stallion is the premier heavy-lift helicopter ever built by the United States government. It is an all-new heavy-lift helicopter that will expand the fleet’s ability to move more material more rapidly. That power comes from three new General Electric T-408 engines, which are more powerful and more fuel efficient than the T-64 engines currently outfitted on the CH-53E.
According to Debbie Cleavenger, PMA-216 assistant program manager engineering and the program office’s chief engineer, three engines created several integration issues, including the most troublesome - exhaust gas re-ingestion (EGR). “EGR occurs when the hot engine gasses are ingested back into the system,” explained Cleavenger. “It can cause anything from increased life-cycle costs, poor engine performance and degradation, time-on-wing decreases, engine overheating and even engine stalls.”
The tiger team’s work began in April 2019, with experts in Engine Performance; Computational Fluid Dynamics; Modeling and Simulation; Materials; Structures; Logistics; Systems Safety; Reliability and Maintainability; Flight Test; and Fire Protection and Survivability completing more than 30 test events and evaluating 135 potential design solutions for engine integration. “The systems constraints were significant,” said Cleavenger. “One change impacted multiple systems.”
Team members worked different root cause analyses in parallel, determining the cause and developing design models to mitigate causes for EGR. From those models, iterative flight testing resulted in a validated model to assess the most promising answer.
That model was then used to construct components for one of the test aircraft that flew a rigorous series of test flights to collect data to validate the model. The extensive set of flight test data was then condensed, analyzed and presented in December 2019 to show that the result performed as predicted and provided an overall design modification that would meet the needs for fleet aircraft. “This is exactly what an integrated test team is supposed to do,” said Perrin. “Bring their expertise to a project, look for resolutions in a dynamic and collaborative environment, determine the best path forward and keep this aircraft on track to the fleet.”
(Image provided with NAVAIR new release)