Wing-Warping Works!
A flight research project that put a 21st century twist on a
century-old technology -- a high-tech derivative of the Wright
brothers' wing-warping method of controlling an aircraft's turning
ability -- can be summed up in two words: "It works!"
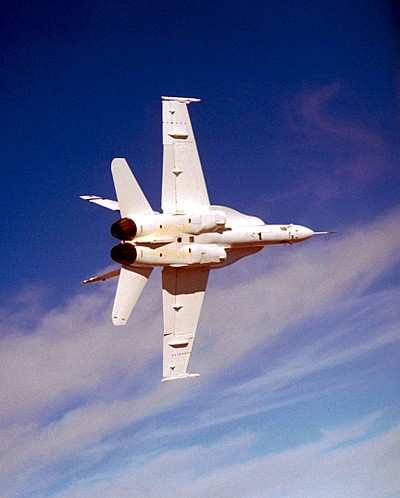
That was the conclusion of project manager Larry Myers as flight
tests in the Active Aeroelastic Wing (AAW) project at NASA's Dryden
Flight Research Center at Edwards Air Force Base, CA, neared their
end.
Jointly sponsored and managed by NASA, the U.S. Air Force
Research Laboratory and Boeing's Phantom Works, the AAW project is
evaluating active control of lighter-weight flexible wings for
improved maneuverability of high-performance military aircraft.
AAW concluded its second phase of flights in early March,
evaluating the ability of software in its flight control computer
to drive its modified control system so that aerodynamically
induced twisting of the wings would provide roll control at
transonic and supersonic speeds. An earlier phase of test flights
conducted in late 2002 and early 2003 provided baseline data on the
flexibility of the modified wing prior to new control laws being
developed and installed. In all, about 80 flights were flown in the
project's two phases. A small number of follow-on flights to
evaluate several other control laws will be flown before the
project concludes flight tests later this month.
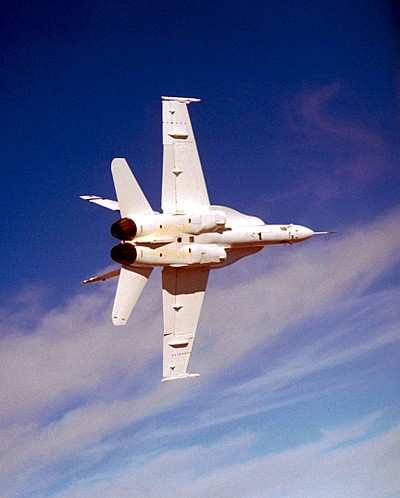
"We have demonstrated a number of subsonic and supersonic flight
conditions where we have actually taken advantage of the
aeroelasticity of the wing," Myers explained. "We've gotten
excellent results, good agreement with a predicted results (and)
roll rates are comparable to what we predicted in simulation. It
looks like we've proven the AAW concept."
"AAW represents a new philosophy for designing highly efficient
wings in terms of structural weight, aerodynamic efficiency and
control effectiveness," said Air Force AAW program manager Pete
Flick, with the AFRL Air Vehicles Directorate at Wright-Patterson
AFB, Ohio.
AAW research flights demonstrated banking or rolling performance
at transonic and supersonic speeds close to that of production
F/A-18s due to wing aeroelastic effects alone, without using
differential stabilator movements to assist in roll control and
with smaller control surface movements.
"We defined 18 test points for this second phase of the flight
test program," explained NASA Dryden AAW project test pilot Dana
Purifoy. "The test points started at 5,000 feet altitude and a
speed of .85 Mach and went out to 25,000 feet and 1.3 Mach, (or 1.3
times the speed of sound). There were small variations on some
points, but in general, we gained good knowledge about what kind of
roll rates we expected to see."
Flick said the benefits of AAW depend on the specific
application.
"With AAW, the control surface deflections can be chosen to
produce an aeroelastic shape that minimizes the load on the
structure (resulting in reduced structural weight), minimizes the
drag of the aircraft (improving fuel efficiency or range), or
maximizes the maneuver rates of the aircraft (enhancing
maneuverability)," he said.
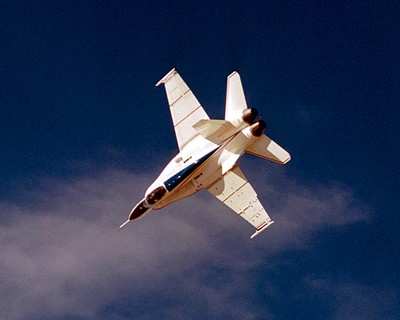
Data obtained from flight tests at Dryden will provide benchmark
design criteria as guidance for a wide variety of future aircraft
design concepts, ranging from high-performance fighters to high
altitude, long endurance UAV concepts, large transport aircraft and
high-speed, long-range aircraft.
The test aircraft-an F/A-18A obtained from the U.S. Navy--was
modified with additional actuators to differentially control the
split leading edge flaps and thinner wing skins that allowed the
outer wing panels to twist up to five degrees. The traditional wing
control surfaces-trailing edge ailerons and leading edge flaps-were
used to provide the aerodynamic force needed to twist or "warp" the
wing.
Extensive instrumentation measured the twisting and bending of
the wing during flight. Numerous strain gauges were installed on
the both wings, along with a flight deflection measurement system
incorporating an optical sensor package in a dorsal pod atop the
fuselage and 16 infrared light emitting diode markers on the upper
surface of the left wing.
The F/A-18's modified wings underwent six months of structural
loads testing in Dryden's Flight Loads Laboratory in 2001. The AAW
F/A-18 then underwent extensive systems tests and simulation before
flight tests began.
Once the flight research is successfully completed, Flick said
the inventors will turn toward spreading the AAW design philosophy
to the technical community.
"Transitioning AAW will likely be a relatively long process
since it represents a design philosophy," he said. "The application
to future (aircraft) will depend on specific design requirements of
those future systems. The benefits are greatest when a vehicle
design is initiated with AAW in mind, and limited when applied to
an existing vehicle."