For Developing Breakthrough Air, Space Technologies
NASA has honored aerospace
industry/US government teams headed by Northrop Grumman Corporation
for developing technologies that could help redefine the economics
of business air travel over land and increase the performance and
payload capabilities of future launch systems.
NASA's Office of Aeronautics honored a Northrop
Grumman/DARPA/NASA team with a 2004 "Turning Goals Into Reality"
(TGIR) award for demonstrating how to decrease the intensity of a
sonic boom by modifying an aircraft's shape. A second Northrop
Grumman/NASA team was recognized with a TGIR award for defining new
ways to manufacture large-scale, high reliability cryogenic fuel
tanks from composite materials.
A third company team received a TGIR award for developing
second-generation reusable launch vehicle concepts. All three
Northrop Grumman teams are part of the company's Integrated Systems
sector.
NASA presents the TGIR awards annually to individuals and teams
that have made substantial contributions to achieving agency-level
goals.Team members will receive their awards July 14 at
presentation ceremonies to be held at NASA headquarters and the
National Air and Space Museum, Steven F. Udvar-Hazy Center in
Chantilly (VA).
"These awards reflect the technological leadership and
collaborative partnership that Northrop Grumman brings to NASA and
the aerospace industry," said Gary Ervin, sector vice president for
Air Combat Systems, a business area of Northrop Grumman's
Integrated Systems sector. "From air to space, from manned to
unmanned systems, we're using that innovative spirit to help our
customers reach their destinations faster, deliver payloads with
greater precision, and return home safely after every mission."
The Northrop Grumman/DARPA/NASA
shaped sonic boom demonstration team will share its TGIR award,
presented in the Partnership award category, with two other NASA
projects that developed new wing technologies. The Northrop
Grumman/NASA cryogenic fuel tank team won its TGIR award for
developing "New Sources of Technology for NASA."
In August 2003, the Northrop Grumman/DARPA/NASA sonic boom team
made aviation history by proving that modifications to the airframe
of a supersonic fighter aircraft could decrease significantly the
intensity of the sonic boom created by that aircraft. Lowering the
intensity of sonic booms could lead to unrestricted supersonic
flight over land, which could speed up commercial business travel
significantly.
The team proved the theory at NASA's Dryden Flight Research
Center at Edwards Air Force Base (CA), by conducting back-to-back
supersonic flight tests of an F-5E with a modified airframe and an
unmodified F-5E aircraft. Comparison of the sound pressure waves
created by the two aircraft showed a significant reduction in sonic
boom intensity for the modified aircraft. Lessons learned from
these test flights could lead to the production of new types of
aircraft with noticeably quieter sonic booms.
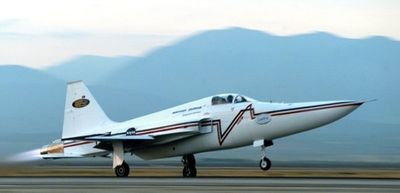
The Northrop Grumman/NASA cryogenic fuel tank team developed and
demonstrated the reliability of new techniques for producing
lightweight, composite structures that could safely contain liquid
hydrogen, an essential but highly volatile rocket fuel that must be
stored and used at minus-423 degrees Fahrenheit. Composite tank
structures, which are 10 to 25 percent lighter than comparably
sized aluminum tanks, will allow rockets and space exploration
vehicles to carry larger payloads.
In November 2003, the team began a test program that will
require a composite test tank structure to be filled with liquid
hydrogen, subjected it to the internal and external loads
experienced during launch, and then drained approximately 40 times.
In 20 cycles to date, the team has detected no leaks in the test
structure, which validates both the structural integrity of the
composite tanks at cryogenic temperatures, and its ability to be
reused.
The Northrop Grumman/NASA team's TGIR award also recognized the
development of a new manufacturing process that enables the
production of large composite structures without an autoclave. An
autoclave is a pressurized oven used to shape, heat and cure
composite structures. To date, one of the biggest barriers to
producing large composite structures has been the cost of building
a suitable autoclave, which is generally proportional to the size
of the structure. Between July 2003 and January 2004, the team
produced and delivered a 10.5-foot-diameter composite fuel tank
half using the non-autoclave process.