Functional Metal With Unique Properties Can Be Trained To Move On Its Own
In the basement of the Materials and Structures Laboratory at NASA’s Glenn Research Center, a shining machine stands so tall it punches a hole through the drop-out ceiling tiles. It has a robust composition of steel pillars and thick metal plates surrounded by wires, dials and knobs. Together, these provide the structure to test a very slight metal rod, no longer than six inches. It seems like quite the production to hold something so minuscule, but this little metal rod is made of a material called shape-memory alloy—and it’s changing the future of flight.
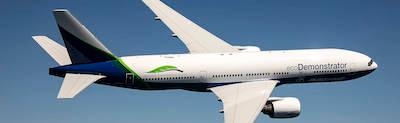
Shape-memory alloy is a functional metal with unique properties that allow it to be trained to move on its own. It’s a functional metal that can go through solid-state phase transformations, meaning it can be stretched, bent, heated, cooled and still remember its original shape. This quality makes the material popular among our scientists; they’ve tested it for several research projects, including Martian rock-splitters and new wheels for NASA’s rovers.
The latest application for this material might be used soon on Earth. Researchers at Glenn have partnered with Boeing to test how shape-memory alloys can be used in deployable vortex generators (VGs), the tiny fins you might have noticed on airplane wings that help control airflow during flight.
Right now, most VGs on airplanes are static. They are fixed devices always present in the airstream to improve performance during takeoff, landing and irregular conditions. But innovations with shape-memory alloys allow for the creation of smart VGs, which move when they sense a change in the environment.
Airplane designers will be able to use this tool to reduce drag throughout the entirety of a flight, improving overall performance, which then translates into direct benefits for passengers. This advancement will make airplanes of the future capable of adjusting in response to changes in temperature, altitude and airspeed, making them more adaptive and more like birds.
Materials Research Engineer Othmane Benafan is part of the team at Glenn developing the shape-memory alloy parts that have been installed on Boeing’s ecoDemonstrator 777. This flying test bed evaluates promising technologies that can solve real-world challenges for airlines, passengers and the environment.
The alloy pieces look like small metal rods that are inserted along the hinge line of a VG where it connects to the aircraft wing. As the shape-memory alloy cools off, it twists. And this twisting motion pulls the fin down to lie flat against the wing. Then as the aircraft moves into warmer conditions, the alloy retracts to its original shape, lifting the fin into an upright position.
“There are no heaters, no coolers,” Benafan said. “The alloys are tuned exactly to environmental temperatures. They sense, and they do their thing.”
The tuning process takes place in the lab at Glenn where Benafan and his team melt alloys from scratch and use the axial torsional machine, mentioned above, to test and train the alloy. The small rod is placed between two grippers that hold it in place while it’s heated, twisted and cooled in an artificial environment that simulates changes in air temperature during flight.
“Sometimes it takes just as long to create the correct testing environment as it takes to make the alloys themselves,” said Materials Research Engineer Darrell Gaydosh. “Along with new alloys, we have built a unique test environment to simulate an aircraft thermal profile throughout the entire flight.”
Tests on the VGs and 49 other technology projects began in early November on the ecoDemonstrator 777. The VG project is still in the early stages, but if the tests are successful, shape-memory alloys can be implemented in aircraft wings to enhance the actuation of many more parts to come. Finding new ways to use this material will greatly improve fuel efficiency, lower carbon dioxide emissions, reduce drag and eventually lead to safer, greener aviation.
As testing progresses, Benafan wants to try using shape-memory alloys in other places of the aircraft where large benefits can be realized. Perhaps the next step is to flex entire aircraft wings to help them move more fluidly as they fly, like we would see in nature.
“The goal is implementation,” Benafan said. “We have come a long way on maturing these materials, and now we want to see them in action. We are getting close.”
(Image provided with NASA news release. Boeing’s ecoDemonstrator 777 is the test bed for new shape-memory alloy technology)