Sat, May 18, 2024
Postaccident Examination Of The Engine Revealed That The Crankshaft Was Fractured At A Crank Cheek
Location: Creswell, Oregon Accident Number: WPR23LA184
Date & Time: May 9, 2023, 17:50 Local Registration: N468MM
Aircraft: RANS S-21 Aircraft Damage: Substantial
Defining Event: Loss of engine power (total) Injuries: 1 None
Flight Conducted Under: Part 91: General aviation - Personal
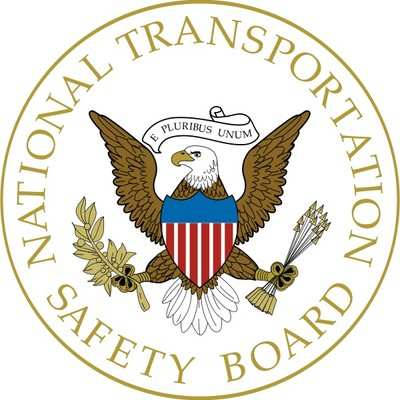
Analysis: The pilot had recently finished building the airplane and it had amassed about 55 hours of flight time on the airframe and engine (A UL Power Engine--Ed). While the pilot was maneuvering at about 700-900 feet above ground level (agl), the engine made “rough” sounds and vibrated. About 20 seconds later the propeller seized and the pilot made a forced landing in the field below.
A postaccident examination of the engine revealed that the crankshaft was fractured at a crank cheek, just aft of the journal of the No. 2 connecting rod. A materials analysis revealed that the crankshaft fracture resulted from fatigue cracks originating at the surface of the aft radius on the No. 2 rod journal, likely due to high operating stresses on the fillet radii. The metallic particles in oil filters suggested continuous wear on the bearing shells. The worn bearing shells most likely intensified the high operating stress in the crankshaft.
The source of the high operating stress acting on the crankshaft and severe wear of the bearings was not determined, but some out of range operating parameters recorded on the Engine Control Unit (ECU) could have contributed or been the source of these stresses, which led to fatigue cracks and severe wear of the bearing shells. Torque for the propeller flange was not measured, but the bolt, though not difficult to remove, likely lost preload torque due to the propeller striking the ground. There was no evidence that the crankshaft failure was a result of a material flaw or defect, and there is no discernible pattern, or recurring failures observed in the six-cylinder engine crankshafts.
Probable Cause and Findings: The National Transportation Safety Board determines the probable cause(s) of this accident to be -- A total loss of engine power caused by fatigue cracking and fracture of the crankshaft due to severe wear of the bearings.
More News
“Honored to accept this mission. Time to take over space. Let’s launch.” Source: SecTrans Sean Duffy commenting after President Donald Trump appointed U.S. Secret>[...]
Permanent Echo Radar signals reflected from fixed objects on the earth's surface; e.g., buildings, towers, terrain. Permanent echoes are distinguished from “ground clutter&rd>[...]
Aero Linx: European Hang Gliding and Paragliding Union (EHPU) The general aim of the EHPU is to promote and protect hang gliding and paragliding in Europe. In order to achieve this>[...]
Glider Encountered A Loss Of Lift And There Was Not Sufficient Altitude To Reach The Airport Analysis: The flight instructor reported that while turning final, the glider encounter>[...]
Airplane Climbed To 100 Ft Above Ground Level, At Which Time The Airplane Experienced A Total Loss Of Engine Power On May 24, 2025, at 1300 eastern daylight time, an Aeronca 7AC, N>[...]