Mon, Jun 18, 2018
Validates 3-D Printing Techniques, According To Aerojet Rocketdyne
Aerojet Rocketdyne recently achieved a significant milestone by successfully completing a series of hot-fire tests of an advanced, next-generation RL10 engine thrust chamber design that was built almost entirely using additive manufacturing; commonly known as 3-D printing.
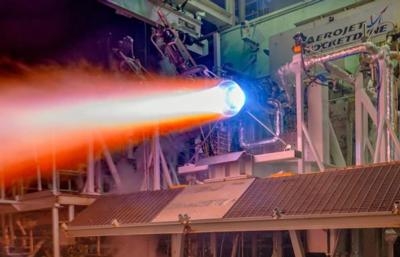
“This recent series of hot-fire tests conducted under our RL10C-X development program demonstrated the large-scale additive manufacturing capability we are maturing to help reduce the cost of this legendary engine system while continuing to provide reliable performance,” said Aerojet Rocketdyne CEO and President Eileen Drake. “This marks another important milestone in our effort to fully qualify components built with additive manufacturing for use in many of our production engine systems.”
The company first demonstrated that a 3-D printed copper alloy thrust chamber and nickel alloy main injector were possible just over a year ago when it completed successful testing of a 3-D printed thrust chamber assembly. The recent round of tests, which took place at the company’s facility in West Palm Beach, Florida, built on the prior work by incorporating a new 3-D printed copper alloy thrust chamber assembly design to accommodate a new re-generatively cooled nozzle that was 3-D printed from a nickel-based alloy.
Current production versions of the RL10 use a complex array of drawn, stainless steel tubes that are brazed together to form a thrust chamber. Incorporating 3-D printing into the process will reduce overall lead time by several months, which in turn will reduce production costs.
“Hot-fire testing helps us validate the approaches we are using to fabricate and join parts that are produced through additive manufacturing to ensure they meet our requirements for materials characterization, structural integrity and durability,” said RL10 Senior Program Director Christine Cooley. “We are also able to accurately define the amount of heat-transfer that is taking place so we can optimize the performance of our next generation of RL10 engines.”
“We continue to look for ways to insert additive manufacturing into our liquid rocket engine designs to not only reduce their cost, but to open up creative design spaces that the additive manufacturing process enables,” added Drake. “This latest round of testing demonstrates that we can systematically print and assemble an engine that can replicate the proven RL10 performance in a fraction of the time and at a reduced cost. Additive manufacturing technology also enables new approaches to engine design that we are now exploring through sub-system testing and validation.”
(Image provided with Aerojet Rocketdyne news release)
More News
Aero Linx: Transport Canada We are a federal institution, leading the Transport Canada portfolio and working with our partners. Transport Canada is responsible for transportation p>[...]
Gross Navigation Error (GNE) A lateral deviation from a cleared track, normally in excess of 25 Nautical Miles (NM). More stringent standards (for example, 10NM in some parts of th>[...]
From AirVenture 2017 (YouTube Edition): Flight-Proven Booster On Display At AirVenture… EAA AirVenture Oshkosh is known primarily as a celebration of experimental and amateu>[...]
Aircraft Parachute System (CAPS) Was Deployed About 293 Ft Above Ground Level, Which Was Too Low To Allow For Full Deployment Of The Parachute System Analysis: The day before the a>[...]
Also: 48th Annual Air Race Classic, Hot Air Balloon Fire, FAA v Banning 100LL, Complete Remote Pilot The news Piper PA-18 Super Cub owners have been waiting for has finally arrived>[...]