Mon, Mar 03, 2014
Experimental Flaps Tested On NASA's Gulfstream G-III
A milestone for the Adaptive Compliant Trailing Edge (ACTE) project at NASA's Dryden Flight Research Center occurred in mid-February with the delivery of two revolutionary experimental flaps designed and built by FlexSys of Ann Arbor, MI, for installation on Dryden’s Gulfstream G-III Aerodynamics Research Test Bed aircraft.
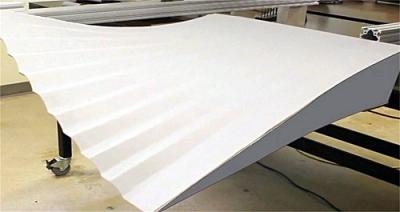
Researchers are preparing to replace the airplane’s conventional 19-foot-long aluminum flaps with advanced, shape-changing assemblies that form continuous bendable surfaces. The new flexible flaps arrived at Dryden by truck on Feb. 12 and were immediately unpacked in preparation for ground vibration testing in NASA Dryden's Flight Loads Laboratory, followed by fit checks and eventual installation.
Technicians have begun scanning the G-III with a special laser system to create a computer-generated 3-D model of the airplane. The flap assemblies will also be scanned so that project engineers can conduct virtual fit checks before actually installing the new flaps. This will reduce the risk of damaging either the airplane or its new control surfaces.
The ACTE experimental flight research project is a joint effort between NASA and the U.S. Air Force Research Laboratory to advance compliant structure technology for use in aircraft to significantly reduce drag, wing weight, and aircraft noise. The effort is part of NASA's Environmentally Responsible Aviation (ERA) project that explores and documents the feasibility, benefits and technical risk of vehicle concepts and enabling technologies to reduce aviation’s impact on the environment.
(Top image: A flexible fluted structure that bridges the gap between the wing root and the shape-changing wing flap that will undergo flight tests on NASA's G-III Aerodynamic Research Test Bed is shown during preliminary tests at FlexSys, Inc. (FlexSys Photo), Bottom NASA aircraft technicians Leo and Juan Salazar work on installation of test instrumentation in preparation for installation of the experimental Adaptive Compliant Trailing Edge flap on NASA's modified G-III Aerodynamic Research Test Bed aircraft.)
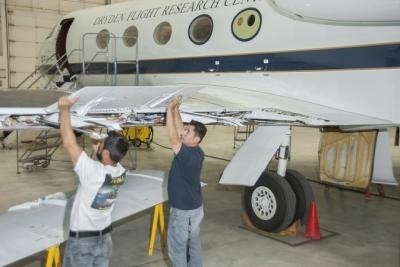
More News
Pilot Applied Full Aft Stick And Nose-Up Trim, But The Airplane Remained On The Runway Analysis: The pilot reported that a preflight inspection and flight control checks revealed n>[...]
A Few Questions AND Answers To Help You Get MORE Out of ANN! 1) I forgot my password. How do I find it? 1) Easy... click here and give us your e-mail address--we'll send it to you >[...]
From 2022 (YouTube Edition): Before They’re All Gone... Humankind has been messing about in airplanes for almost 120-years. In that time, thousands of aircraft representing i>[...]
Advanced Air Mobility (AAM) A transportation system that transports people and property by air between two points in the NAS using aircraft with advanced technologies, including el>[...]
Aero Linx: MQ-1B Predator The MQ-1B Predator is an armed, multi-mission, medium-altitude, long-endurance remotely piloted aircraft that is employed primarily as an intelligence-col>[...]