Applicability: All owners,
operators and maintainers of Textron Lycoming piston engines.
Background: CASA has developed a database to
review and analyse bearing failures on piston engines. This
Bulletin captures the underlying reasons for bearing failures and
recommends steps to minimize recurrence.
Bearing Construction
A plain bearing, largely used in piston engines, consists of two
semicircular steel shells, providing a closed circular housing for
crankshaft main and piston rod big-end journal. The shell has
lubrication holes for oil flow and dowel locating holes for correct
alignment and retention. The outermost steel shell provides
strength while the inner layers provide other desirable features
such as "fatigue strength" and the ability to form itself.
Plain bearings supplied prior to 1995 were "copper cast." While
all specifications are indicative and actual composition remains
proprietary formula, a typical 'copper cast' bearing would have a
steel outer shell, deposited with a thick layer of an alloy of
copper (80%), lead (15%) & tin (5%). The copper-lead layer will
then have a very thin (1 to 2 micrometer) nickel dam to stop the
flow of tin, followed by a Babbitt layer.
The Babbitt layer (also called white
metal) is a 25-30 micrometer thick sacrificial material layer
comprising lead (88%), tin (9%) and copper (3%). White metal is
relatively soft and has a low melting point. Babbitt "forms" itself
to a perfect-fit with respect to crankshaft and crankcase by
"settling-in." It also allows embedding of small debris present in
oil due to its softness and reduces scoring of crankshaft main and
piston connecting rod journals.
"Aluminum-cast" plain bearings were introduced in the late
1990s. They consist of a steel shell deposited with a layer of
aluminium (95%) and tin (5%). The nickel dam and Babbitt layers are
then deposited on an aluminium layer and are similar to that on
'copper cast' bearings.
Available data indicates that "aluminium cast" bearings have
lower durability when compared to "copper cast" bearings. KS
Bearing Inc of Indiana in the USA mostly supplied aluminium cast
bearings. Textron Lycoming switched back to copper-cast bearings in
1999-2000 with a modified composition and has made a gradual shift
to these new bearings since then. (Reference Lycoming Service
Bulletins 544, 544A, 547, 547 supp 1, Special Advisory 59-800 and
SB 561 and SI 1512.) Other PMA bearing suppliers have also
confirmed their switch to copper cast/trimetal bearings.
Engine OperationsFuel–air ratio, ignition timing, charge
temperature and BMEP (Break Mean Effective Pressure) (BMEP) are
four critical variables that can adversely affect bearing
durability.
Operating with the lean fuel–air ratio may mean give
better economy but it may also mean engine deterioration. Lean
mixture burns more slowly, has a lower maximum temperature and may
cause valve overheating and deformation. Consequently engine
malfunction can adversely affect bearing durability.
Assuming that the ignition is correctly timed, many other
factors like deposition of combustion products inside the
combustion chamber may also cause "pre-ignition." Engines operating
on leaded fuel form deposits of "lead oxy-bromide" inside
cylinders. Lead oxy-bromide and/or unburnt carbon deposits inside a
combustion chamber create 'hot spots' and may cause
pre-ignition.
Pre-ignition and detonation may
cause can lead engine to engine overheat and which may burn the
holes in pistons or the combustion chamber. The rapid increase in
pressures associated with detonation can cause lubrication
breakdown and subsequent bearing failure.
Maintenance
Plain bearings operate with a hydrodynamic lubricating film
provided by oil supplied under pressure. When the oil film breaks
down, metal-to-metal contact generates excess heat, which may cause
the white metal portion of the bearing to melt and then resolidify
in "cooler" parts of the bearing. Re-deposited bearing material
does not form a metallurgical bond with the underlying material and
can be easily peeled off. Circumferential scoring of such bearing
surface usually occurs. This phenomenon will also occur if the
temperature in the oil film rises above the melting point of the
white metal bearing material.
There are a number of possible factors that eventually lead to
bearing failure:
- Inadequate supply of oil due to malfunctioning oil pump, low
oil level or restriction in lubrication lines.
- Inadequate bearing clearances.
- Use of inappropriate lubricant.
- Blockage or restriction in oil-coolers or any factor leading to
ineffective cooling.
- Loss of bearing area and stress concentration due to
pre-existing defects.
- Unapproved operating procedures.
- Engine baffles not correctly sealed or insufficient amount of
cooling-air to cylinder cooling fins.
- Incorrect ignition timing.
- Incorrect adjustment of mixture for the engine power setting
during engine ground runs and in operation.
- Propeller strike.
- Failure to 'break-in' the engine.
The purpose for engine break-in is to set the piston rings,
stabilize the oil consumption and maintain bearing clearances after
piston rings / cylinders replacement or honing (as in field
overhaul) or after an engine installation on the aircraft for the
first time following shop assembly. Failure to pre-oil the engines
before the first start, whenever there is an engine change, oil
cooler replacement or draining or any prolonged period of
inactivity. Keeping an eye out for the signs of impending bearing
failure through proper inspection of oil, filters and engine
general condition may help identify signs of an impending engine
failure.
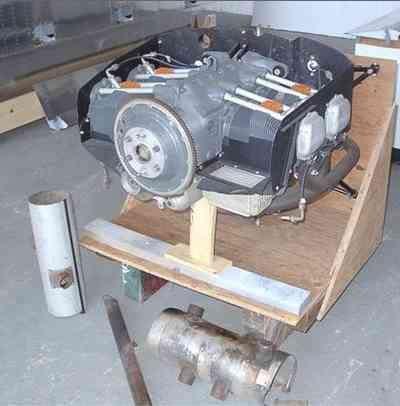
Assembly/Overhaul Practices
The crankcase bearing locating diameters, crankshaft main
diameters and piston connecting rod internal diameters must be
within manufacturer's dimensions and tolerances with no planar
discontinuity in the journal surface. Any high spots, eccentricity
or axial asymmetry of major diameters will result in uneven bearing
loading, lower contact area, higher stress concentration, leading
to white metal overheat and displacement resulting in bearing
failure.
Similarly "lack of bearing crush" may result in bearing
rotation, fretting and failure. Conformance to manufacturer's
recommended overhaul procedures, materials and standard practices
can never be over-emphasized.
Recommendations
For Engine Overhaul Shops:
- Incorporate Lycoming Service Bulletins 544A, 547 supp 1 , and
561 and SI 1512 (or later Service literature Bulletins related to
bearings), as applicable.
- During overhaul, ensure a high degree of cleanliness of the
bearing areas.
- Ensure proper retention of bearing inserts by correct
dowelling.
- Ensure correct bearing crush between the shell and the
crankcase or the connecting rod.
For Maintenance Personnel:
-
Change oil and filter and carry out
inspection per provisions of Lycoming SB 480D. Cutting the filter
open and inspecting contents may provide valuable information on
impending engine failure. CASA recommends that when carrying out
the engine oil and oil filter change procedure detailed in Textron
Lycoming SB 480D, drain the oil whilst the engine is still hot and
strain the hot oil through a fine mesh screen filter. Draining the
oil whilst it is hot will assist in flushing out bearing material
flakes.
- Ensure correct sealing of engine baffles and keep cooling-air
passages to cylinder cooling fins clear. If there is any sign of
engine, cylinder or piston overheat, carry out a full inspection of
the piston and cylinder assembly.
- Perform engine break-in per provisions of Lycoming Service
Instruction SI 1427B (or the latest revision), if applicable.
- Pre-oil the engine per provisions of Lycoming Service
Instruction SI 1241C or the latest revision, before the first
start, whenever there is an engine change, oil cooler replacement
or draining , or any prolonged period of inactivity.
- Ensure correct functioning of engine lubrication systems.
- Ensure correct ignition timing.
- Ensure correct adjustment of mixture for the engine power
setting during engine ground runs and in operation.
Use clean, clear and contamination-free fuels, oils and additives
as per aircraft flight manual (AFM).
In case of doubt, contact your overhaul facility or
manufacturer.
Pilots/Flight Operations:
- Use fuel-air mixture as per approved POH/AFM.
- Report all instances of engine malfunction, exceeded parameters
and propeller strike, even if they are minor.