Engineers From Around The World Leave Jury Of Aerospace Experts Impressed With Submissions
Following a month-long, highly competitive engineering competition, the winners of the Stratasys CubeSat Challenge have been announced.
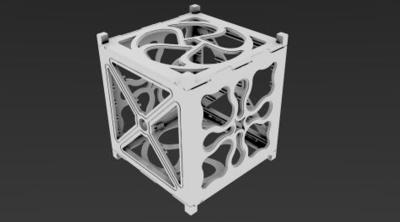
Stratasys, which provided 3D printing and additive manufacturing solutions, along with its subsidiaries GrabCAD and MakerBot, sponsored the competition.
The GrabCAD Community was invited to use 3D printing to rethink the design of a CubeSat, a standardized small satellite frame originally developed to allow university students to build low-cost satellites for research and education purposes. The goal was to design CubeSat structures that would be faster and easier to manufacture, and pack more utility into the very small volume that CubeSat designers had to work with. Participants had the chance to win prizes that range from MakerBot Replicator Desktop 3D Printers to cash to manufacturing services provided by Stratasys Direct Manufacturing.
Over 200 entries were submitted from all engineering disciplines and geographic locations. The submissions demonstrate the ability of additive manufacturing to vastly improve design over traditional manufacturing methods. “Engineers were able to reduce satellite structures from up to 50 parts down to two or three parts by using additive manufacturing,” said Scott Sevcik, business development manager for aerospace and defense at Stratasys. “There were a number of very creative approaches to redesigning the satellite structure, and it was great to see several of the entries consolidate the build down to two or as few as one part. That highlights one of the most significant benefits of 3D printing a structure.
Reducing part count from 50 to three can make a significant impact on a manufacturer’s operations. It can:
- Reduce the amount of assembly labor, which saves cost and time.
- Reduce the risk of assembly error, or a late part delaying production.
- Reduce the risk of repetitive stress and other ergonomic injuries due to assembly effort.
- Simplify the supply chain, reducing purchasing, receiving inspection and other ancillary risks and costs.
First place was awarded to Paolo Minetola for his entry FoldSat, a design that uses geometries only possible with 3D printing. Second place went to David Franklin for his entry STRATASATT – FDM ONE, a design that illustrates customization using real CubeSat components. Third place went to Chris Esser with his entry Foldable Articulated CubeSat for Additive Manufacturing. His design featured 3D printed threads and six hinged panels.
Entries were judged based on technical requirements including feasibility, production, value and being optimized for additive manufacturing. The judging panel included experts from the aerospace and 3D printing industry:
- Dr. Jordi Puig-Suari, Cal Poly Professor and Co-Inventor of the CubeSat Standard
- Dr. Robert Hoyt, CEO and Chief Scientist, Tethers Unlimited Inc.
- David Espalin, Center Manager - W.M. Keck Center for 3D Innovation, University of Texas, El Paso
- Adam Hadaller, Mission Manager, Spaceflight Industries
- Patrick Price, Aerospace Additive Manufacturing Research Engineer, Stratasys
- Jesse Marin, Aerospace Project Engineer, Stratasys Direct Manufacturing
- Jonathan Cook, Director of Product, MakerBot
The Aerospace vertical solutions team sponsored the CubeSat Challenge, with collaboration from GrabCAD, MakerBot and Stratasys Direct Manufacturing.
(Images provided by Stratasys. First place was Paolo Minetola for FoldSat, a design that uses geometries only possible with 3D printing. Photo by Paolo Minetola)