Thu, Jun 28, 2012
German Scientists Flight Test A New Main Rotor Blade Developed After Studying The Leviathans
Modern helicopters could be significantly faster and more maneuverable - if aerodynamics did not impose limitations on them. That's the conclusion reached by researchers at the German Aerospace Center (Deutsches Zentrum für Luft- und Raumfahrt; DLR) in Göttingen, who earlier this year discovered and flight-tested a way to increase maneuverability using an idea they got from observing humpback whales.
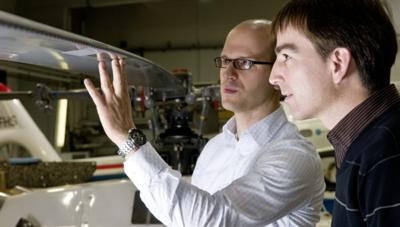
The scientists found that there are to aerodynamic disadvantages to a helicopter's main rotor. The airflow over a backward-moving main rotor blade separating from the aerofoil during fast forward flight or maneuvering ... a 'dynamic stall' ... creates turbulence, loss of lift and exerts large forces on the rotor. Drag increases and the rotor head control rods are subjected to large dynamic loads. "This limits the top speed of helicopters at high altitude and, in particular, their maneuverability," explains Kai Richter from the DLR Institute of Aerodynamics and Flow Technology in Göttingen. In addition, the resulting vibration often translates to passenger comfort. The DLR scientists say modern engines would be able to deliver significantly better flight performance were it not for these limitations. "Stalling is one of the most serious problems in helicopter aerodynamics – and one of the most complex," says Richter. Generating a computer simulation of a moving rotor is significantly more
complicated than modelling a fixed-wing aircraft.
When looking for ways to delay the onset of stalling in helicopters, researchers at Göttingen struck gold with humpback whales - which is somewhat surprising at first glance. "These marine mammals are renowned for their great speed and acrobatic skills," says Holger Mai from the DLR Institute of Aeroelasticity. This is due to their unusually large pectoral fins, which have characteristic bumps along the front edge. "Research has shown that these bumps cause stalling to occur significantly later underwater and increase buoyancy."
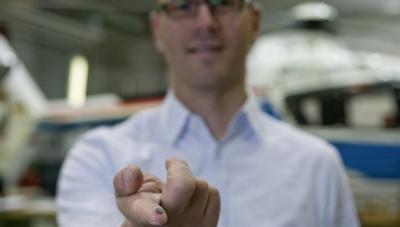
DLR researchers translated the idea of using bumps for delaying the onset of stalling to helicopter rotors, and patented it as Leading-Edge Vortex Generators (LEVoGs) "Flow phenomena in water are similar to those in air; they just need to be scaled accordingly," says Mai. The artificial bumps on helicopters are smaller than those on a humpback whale; they have a diameter of six millimetres and weigh just 0.04 grams.
Experiments conducted in the wind tunnel were promising, enabling a test flight using the DLR Bo 105 research helicopter in Braunschweig to be successfully carried out, as part of the DLR SIMCOS (Advanced Simulation and Control of Dynamic Stall) project. 186 rubber LEVoGs were glued to each of the helicopter’s four rotor blades.
"The pilots ... noticed a difference in the behavior of the rotor blades," says Richter. The main objective of the initial test flight was to demonstrate the safety of this new technique. "The next step is a flight using special measuring equipment to accurately record the effects," Richter said in a news release following the experiment.
Deutsche Welle reports that the next step in the research will be to fly a helicopter with a rotor blade into which 100 tiny holes have been drilled, each fitted with a sensor to measure pressure.
If the concept proves successful, DLR researchers hope that existing helicopters could be retrofitted at little expense. For new helicopters, contours could be milled into the front edges of existing titanium blade designs during the manufacturing process. (Pictured: Top: LEVoG. Bottom L-R Kai Richter, Holger Mai inspect rotor blade fitted with LEVoGs. Bottom, LEVoG on a fingertip. Images provided by DLR)
More News
Capsized Vessel Located Near Dauphin Island, Alabama The Coast Guard rescued four boaters after their vessel capsized near Dauphin Island, Alabama, Thursday. Coast Guard District E>[...]
Reserve Components Looking to Improve In-House General Atomics Aeronautical Systems announced a fresh order for a dozen Gray Eagle 25M UAVs with accompanying equipment, for fulfill>[...]
Brand New! Avoid The Need For A Comeback... Get Your Marketing Right, Right Now! Some time ago, the Aero-News Network, responding to numerous requests, established a marketing and >[...]
Also: Hubble On Pause, FedEx Pilots Picket, Nexus eVTOL, VFS Honors The Rotax folks have published a Service Bulletin after issues were noted that may affect all R915i and R916i se>[...]
John W. Winter of AEA and Avionic Fame Passes John W. Winter brought Mid-Continent Instrument Company into the modern era in 1980, purchasing the firm and using it as a base for ex>[...]