What They Had Was '...a Failure to Lubricate'
There are a lot of lessons here -- some about
flying, but particularly about maintenance.
Everything is important; a little mistake can have great
consequences; cleanliness and lubrication are critical;
properly-designed tooling can make the difference; scientific
testing needs to precede changes in maintenance procedures; the
acceptable application of two different lubricants does not
necessarily mean the two lubes are compatible with each other;
and when you're in an emergency flight mode and find some
tactic that works, stick with it.
Here's what happened, straight from the NTSB:
1. The flight crewmembers on Alaska Airlines flight 261 were
properly certificated and qualified and had received the training
and off-duty time prescribed by Federal regulations. No evidence
indicated any preexisting medical or other condition that might
have adversely affected the flight crew's performance during the
accident flight.
2. The airplane was dispatched in accordance with Federal
Aviation Administration regulations and approved Alaska Airlines
procedures. The weight and balance of the airplane were within
limits for dispatch, takeoff, climb, and cruise.
3. Weather was not a factor in the accident.
4. There was no evidence of a fire or of impact with birds or
any other foreign object.
5. No evidence indicated that the airplane experienced any
preimpact structural or system failures, other than those
associated with the longitudinal trim control system, the
horizontal stabilizer, and its surrounding structure.
6. Both engines were operating normally before the final
dive.
7. Air traffic control personnel involved with the accident
flight were properly certificated and qualified for their assigned
duty stations.
8. The longitudinal trim control system on the accident airplane
was functioning normally during the initial phase of the accident
flight.
9. The horizontal stabilizer stopped responding to
autopilot and pilot commands after the airplane passed through
23,400 feet. The pilots recognized that the longitudinal trim
control system was jammed, but neither they nor the Alaska Airlines
maintenance personnel could determine the cause of the jam.
10. The worn threads inside the horizontal stabilizer acme nut
were incrementally sheared off by the acme screw and were
completely sheared off during the accident flight. As the airplane
passed through 23,400 feet, the acme screw and nut jammed,
preventing further movement of the horizontal stabilizer until the
initial dive.
11. The accident airplane's initial dive from 31,050 feet began
when the jam between the acme screw and nut was overcome as a
result of operation of the primary trim motor. Release of the jam
allowed the acme screw to pull up through the acme nut, causing the
horizontal stabilizer leading edge to move upward, thus causing the
airplane to pitch rapidly downward.
12. The acme screw did not completely separate from the acme nut
during the initial dive because the screw's lower mechanical stop
was restrained by the lower surface of the acme nut until just
before the second and final dive about 10 minutes later.
13. The cause of the final dive was the low-cycle fatigue
fracture of the torque tube, followed by the failure of the
vertical stabilizer tip fairing brackets, which allowed the
horizontal stabilizer leading edge to move upward significantly
beyond what is permitted by a normally operating jackscrew
assembly. The resulting upward movement of the horizontal
stabilizer leading edge created an excessive upward aerodynamic
tail load, which caused an uncontrollable downward pitching of the
airplane from which recovery was not possible.
14. In light of the absence of a checklist requirement to land
as soon as possible and the circumstances confronting the flight
crew, the flight crew's decision not to return to Lic Gustavo Diaz
Ordaz International Airport, Puerto Vallarta, Mexico, immediately
after recognizing the horizontal stabilizer trim system malfunction
was understandable.
15.
The flight crew's decision to divert the flight to Los Angeles
International Airport, Los Angeles, California, rather than
continue to San Francisco International Airport, San Francisco,
California, as originally planned was prudent and appropriate.
16. The flight crew's use of the autopilot while the horizontal
stabilizer was jammed was not appropriate.
17. The captain should have kept the slats and flaps
extended when the airplane was found to be controllable in that
configuration after the initial dive. (TO BE REVISED)
18. Without clearer guidance to flight crews regarding which
actions are appropriate and which are inappropriate in the event of
an inoperative or malfunctioning flight control system, pilots may
experiment with improvised troubleshooting measures that could
inadvertently worsen the condition of a controllable airplane.
19. The acme nut threads on the accident airplane's horizontal
stabilizer jackscrew assembly wore at an excessive rate.
20. Alaska Airlines' use of Aeroshell 33 for lubrication of the
jackscrew assembly, acme screw thread surface finish, foreign
debris, and abnormal loading of the acme nut threads were not
factors in the excessive wear of the accident acme nut threads.
21. There was no effective lubrication on the acme screw and nut
interface at the time of the Alaska Airlines flight 261
accident.
22. The excessive and accelerated wear of the accident jackscrew
assembly acme nut threads was the result of insufficient
lubrication, which was directly causal to the Alaska Airlines
flight 261 accident.
23. Alaska Airlines' extension of its lubrication interval for
its McDonnell Douglas MD-80 horizontal stabilizer components, and
the FAA's approval of that extension, the last of which was based
on Boeing's extension of the recommended lubrication interval
increased the likelihood that a missed or inadequate lubrication
would result in excessive wear of jackscrew assembly acme nut
threads and, therefore, was a direct cause of the excessive wear
and contributed to the Alaska Airlines flight 261 accident.
24. When lubricating the jackscrew assembly, removal of used
grease from the acme screw before application of fresh grease will
increase the effectiveness of the lubrication.

25. A larger access panel would facilitate the proper
accomplishment of the jackscrew assembly lubrication task.
26. If the jackscrew assembly lubrication procedure was a
required inspection item for which an inspector's signoff is
needed, the potential for unperformed or improperly performed
lubrications would be reduced.
27. Alaska Airlines' extension of the end play check interval,
and FAA's approval of the extension, allowed the accident acme nut
threads to wear to failure without the opportunity for detection
and, therefore, was a direct cause of the excessive wear and
contributed to the Alaska Airlines flight 261 accident.
28. Alaska Airlines' end play check interval extension should
have been, but was not, supported by adequate technical data to
demonstrate that the extension would not present a potential
hazard.
29. The existing process by which manufacturers revise
recommended maintenance task intervals and by which airlines
establish and revise these intervals does not include task-by-task
engineering analysis and justification and, therefore, allows for
the possibility of inappropriate interval extensions for
potentially critical maintenance tasks.
30.
Because of the possibility that higher-than-expected wear could
cause excessive wear in less than 2,000 flight hours and the
additional possibility that an end play check could be unperformed
or improperly performed, the current 2,000-flight-hour end play
check interval specified in Airworthiness Directive 2000-15-15 may
be inadequate to ensure the safety of the Douglas DC-9, McDonnell
Douglas MD-80/90, and Boeing 717 fleet.
31. The continued collection and analysis of end play data are
critical to monitoring acme nut thread wear and identifying
excessive or unexpected wear rates, trends, or anomalies.
32. Until August 2000, Alaska Airlines used a fabricated
restraining fixture that did not meet Boeing specifications;
however, the Safety Board could not determine whether the use of
this noncompliant fixture generated an inaccurate end play
measurement during the last end play check or whether the use of
this fixture contributed to the accident.
33. The on-wing end play check procedure, as currently
practiced, has not been validated and has low reliability.
34. Deficiencies in the overhaul process increase the likelihood
that jackscrew assemblies may be improperly overhauled.
35. The absence of a requirement to record or inform customers
of the end play measurement of an overhauled jackscrew assembly
could result in an operator unknowingly returning a jackscrew
assembly to service with a higher-than-expected end play
measurement.
36. Operators will maximize the usefulness of end play
measurements and wear rate calculations by recording on-wing end
play measurements whenever a jackscrew assembly is replaced on an
airplane.
37. Because the jackscrew assembly is an integral and essential
part of the horizontal stabilizer trim system, a critical flight
system, it is important to ensure that maintenance facilities
authorized to overhaul these assemblies possess the proper
qualifications, equipment and documentation.
38. The dual-thread design of the acme screw and nut does not
provide redundancy with regard to wear.
39.
The design of the Douglas DC-9, McDonnell Douglas MD-80/90, and
Boeing 717 horizontal stabilizer jackscrew assembly did not account
for the loss of the acme nut threads as a catastrophic single-point
failure mode. The absence of a fail-safe mechanism to prevent the
catastrophic effects of total acme nut thread loss contributed to
the Alaska Airlines flight 261 accident.
40. When a failure could have catastrophic results, it is
not appropriate to rely on maintenance and inspection intervention
to prevent the failure from occurring if a practicable design
alternative could eliminate the catastrophic effects of the failure
mode. (TO BE REVISED)
41. Douglas DC-9, McDonnell Douglas MD-80/90, and Boeing 717
series airplanes, and if found necessary other transport category
airplanes, should be modified to ensure that loss of the horizontal
stabilizer trim system's jackscrew assembly acme nut threads or
other control assembly does not preclude continued safe flight and
landing.
42. Catastrophic single-point failure modes should be prohibited
in the design of all future airplanes with horizontal stabilizer
trim systems, regardless of whether any element of that system is
considered structure rather than system or is otherwise considered
exempt from certification standards for systems.
43. The certification requirements applicable to
transport-category airplanes should fully consider and address the
consequences of failures resulting from wear.
44. At the time of the flight 261 accident, Alaska Airlines'
maintenance program had widespread systemic deficiencies.
45. The FAA did not fulfill its responsibility to properly
oversee the maintenance operations at Alaska Airlines, and at the
time of the Alaska Airlines flight 261 accident, Federal Aviation
Administration surveillance of Alaska Airlines had been deficient
for at least several years.
Probable Cause
The National Transportation Safety Board determines that the
probable cause of this accident was a loss of airplane pitch
control resulting from the in-flight failure of the horizontal
stabilizer trim system jackscrew assembly's acme nut threads. The
thread failure was caused by excessive wear resulting from Alaska
Airlines' insufficient lubrication of the jackscrew assembly.
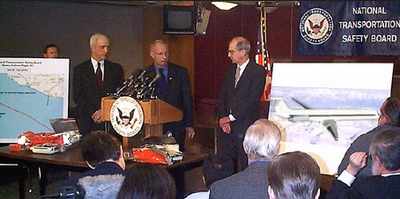
Contributing to the accident was
(1) Alaska Airlines' extended lubrication interval, and the FAA's
approval of that extension, which increased the likelihood that an
unperformed or inadequate lubrication would result in excessive
wear of the acme nut threads; and
(2) Alaska Airlines' extended end play check interval, and the
FAA's approval of that extension, which allowed the excessive wear
of the acme nut threads to progress to failure without the
opportunity for detection. Contributing also to the accident was
the absence on the MD-80 of a fail-safe mechanism to prevent the
catastrophic effects of total acme nut thread loss.
--
Perhaps even more-importantly in the long run, the NTSB had a
number of safety recommendations:
As a
result of the investigation of the Alaska Airlines flight 261
accident, the National Transportation Safety Board makes the
following recommendations to the Federal Aviation
Administration:
1. Issue a flight standards information bulletin directing air
carriers to instruct pilots that in the event of an inoperative or
malfunctioning flight control system, if the airplane is
controllable they should complete only the applicable checklist
procedures and should not attempt any corrective actions beyond
those specified. In particular, in the event of an inoperative or
malfunctioning horizontal stabilizer trim control system, after a
final determination has been made in accordance with the applicable
checklist that both the primary and alternate trim systems are
inoperative, neither the primary nor the alternate trim motor
should be activated, either by engaging the autopilot or using any
other trim control switch or handle. Pilots should further be
instructed that if checklist procedures are not effective, they
should land at the nearest suitable airport. (A-02-XX)
2. As part of the response to Safety Recommendation A-01-41,
require operators of Douglas DC-9, McDonnell Douglas MD-80/90, and
Boeing 717 series airplanes to remove degraded grease from the
jackscrew assembly acme screw and flush degraded grease and
particulates from the acme nut before applying fresh grease.
(A-02-XX)
3. As part of the response to Safety Recommendation A-01-41,
require operators of Douglas DC-9, McDonnell Douglas MD-80/90, and
Boeing 717 series airplanes, in coordination with Boeing, to
increase the size of the access panels that are used to accomplish
the jackscrew assembly lubrication procedure. (A-02-XX)
4. Establish the jackscrew assembly lubrication procedure as a
required inspection item that must have an inspector's signoff
before the task can be considered complete. (A-02-XX)
5.
Review all existing maintenance intervals for tasks that could
affect critical aircraft components and identify those that have
been extended without adequate engineering justification in the
form of technical data and analysis demonstrating that the extended
interval will not present any increased risk and require
modifications of those intervals to ensure that they (1) take into
account assumptions made by the original designers, (2) are
supported by adequate technical data and analysis, and (3) include
an appropriate safety margin that takes into account the
possibility of missed or inadequate accomplishment of the
maintenance task. In conducting this review, the Federal Aviation
Administration should also consider original intervals recommended
or established for new aircraft models that are derivatives of
earlier models and, if the aircraft component and the task are
substantially the same and the recommended interval for the new
model is greater than that recommended for the earlier model, treat
such original intervals for the derivative model as "extended"
intervals. (A-02-XX)
6. Conduct a systematic industrywide evaluation and issue a
report on the process by which manufacturers recommend and airlines
establish and revise maintenance task intervals and make changes to
the process to ensure that, in the future, intervals for each task
(1) take into account assumptions made by the original designers,
(2) are supported by adequate technical data and analysis, and (3)
include an appropriate safety margin that takes into account the
possibility of missed or inadequate accomplishment of the
maintenance task. (A-02-XX)
7. Require operators to supply the Federal Aviation
Administration, before the implementation of any changes in
maintenance tasks intervals that could affect critical aircraft
components, technical data and analysis for each task demonstrating
that none of the proposed changes will present any potential
hazards, and obtain written approval of the proposed changes from
the principal maintenance inspector and written concurrence from
the appropriate FAA aircraft certification office. (A-02-XX)
8. Pending the incorporation of a fail-safe mechanism in the
design of the Douglas DC-9, McDonnell Douglas MD-80/90, and Boeing
717 horizontal stabilizer jackscrew assembly, as recommended in
[Safety Recommendation 13 in this report], establish an end play
check interval that (1) accounts for the possibility of
higher-than-expected wear rates and measurement error in estimating
acme nut thread wear and (2) provides for at least two
opportunities to detect excessive wear before a potentially
catastrophic wear condition becomes possible. (A-02-XX)
9. Require operators to permanently (1) track end play measures
according to airplane registration number and jackscrew assembly
serial number, (2) calculate and record average wear rates for each
airplane based on end play measurements and flight times, and (3)
develop and implement a program to analyze these data to identify
and determine the cause of excessive or unexpected wear rates,
trends, or anomalies. The Federal Aviation Administration (FAA)
should also require operators to report this information to the FAA
for use in determining and evaluating an appropriate end play check
interval. (A-02-XX)
10. Require that maintenance facilities that overhaul jackscrew
assemblies record and inform customers of an overhauled jackscrew
assembly's end play measurement. (A-02-XX)
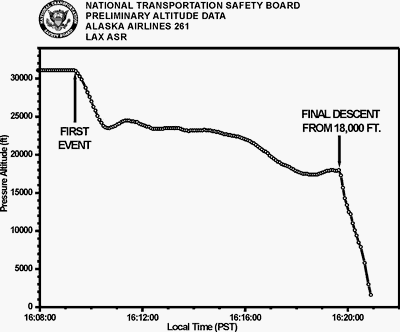
11. Require operators to measure and record the on-wing end play
measurement whenever a jackscrew assembly is replaced.
(A-02-XX)
12. Require that maintenance facilities that overhaul Douglas
DC-9, McDonnell Douglas MD-80/90, and Boeing 717 series jackscrew
assemblies obtain specific authorization to perform such overhauls,
predicated on demonstrating that they possess the necessary
capability, documentation, and equipment for the task and that they
have procedures in place to (1) perform and document the detailed
steps that must be followed to properly accomplish the end play
check procedure and lubrication of the jackscrew assembly,
including specification of appropriate tools and grease types; (2)
perform and document the appropriate steps for verifying that the
proper acme screw thread surface finish has been applied; and (3)
ensure that appropriate packing procedures are followed for all
returned overhauled jackscrew assemblies, regardless of whether the
assembly has been designated for storage or shipping. (A-02-XX)
13. Conduct a systematic engineering review of all transport
category airplanes to identify means to eliminate the catastrophic
effects of a system or associated structure failure in the
horizontal stabilizer trim system jackscrew assembly, and, if
practical, that all future transport category airplanes incorporate
such fail-safe mechanisms. (A-02-XX) (TO BE REVISED)
14. Modify the certification regulations, policies, or
procedures to ensure that new horizontal stabilizer trim control
system designs are not certified if they have a single-point
catastrophic failure mode, regardless of whether any element of
that system is considered structure rather than system or is
otherwise considered exempt from certification standards for
systems. (A-02-XX)
15. Review and revise aircraft certification
regulations and associated guidance applicable to the certification
of transport-category airplanes to ensure that wear-related
failures are fully considered and addressed so that, to the maximum
extent possible, they will not be catastrophic. (A-02-XX)
16. Issue a Flight Safety Information Bulletin directing air
carriers to discourage their dispatch and maintenance control
personnel from engaging in in-flight trouble shooting. (A-02-XX)
(TO BE REVISED)
[That's what happened, according to the best accident
investigators in the world. Now, the lawyers will tell juries what
"really" happened, as they look for the deepest pockets (to empty
into their own). Thus, money that could be spent on improving
safety will be used to pay off "punitive" lawsuits, helping ensure
a long-lasting revenue stream of blood money to law
firms --ed.]