During flight-testing of
their new gyro prototype just prior to New Year's Day, Carter
Aviation Technologies (Carter) reports that their test pilot,
George Mitchell, executed several vertical take-offs where the
aircraft was able to jump more than 150 feet straight up into the
air. According to Mitchell, "It was phenomenal! But, it took a
little getting used to. It's not something you do with the average
gyro. The "g" meter showed 2.25 Gs on take-off!" The amazing
take-offs were the result of a new rotor system that Carter
developed for the gyro.
Although the new rotor system was pit-tested to 670 rpm (on a
Corvette engine) initial flight-tests began with the rotor rpm well
under maximum. As George became more comfortable with the safety
aspects of the new rotor system he began testing its capability.
One of the first tests was an aborted take-off at minimum jump
take-off rpm to prove that the stored energy in the rotor was
enough to safely return the pilot to the ground. The test video
shows it worked perfectly.
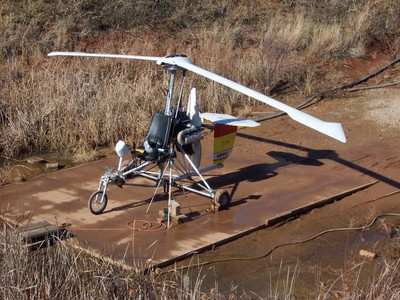
Next, he performed a near vertical landing approach and then
applied full throttle just feet from the ground for a go-around.
Again, the system proved its capability. As Mitchell developed more
confidence the rotor rpm was increased to a maximum 490 rpm. It was
then that the take-off angle increased to true vertical for 150
feet. If the aircraft was allowed to accelerate forward after the
jump take-off it achieved an altitude of about 300 feet before the
rotor rpm slowed to cruise.
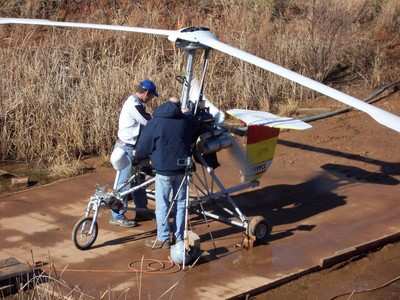
Carter President and CEO, Jay Carter, Jr., was visibly excited.
His first comments were, "This is awesome! Now we can show that our
basic technology has applications beyond our own designs."
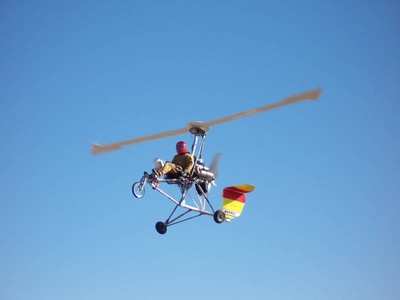
The recent flight-tests were a culmination of a series of
flight-tests set to prove the capability of several of Carter's
basic technological developments. In late 2004 Carter purchased a
stock autogyro kit and began integrating their technology into the
building of the aircraft. Previously, all of Carter's technology
was incorporated into their own prototype so there was no direct
comparison of their technology to what was available in the
industry. Carter felt this comparison was important to validate
their technology. The new gyro prototype was termed the CarterGyro
Demonstrator/Trainer (CGD/T or CarterGyro). Carter first added
their patented landing gear. The gear has a 14-inch stroke and has
the ability to absorb a landing impact of up to 6.0 Gs (thus far
only 3.5 Gs have been recorded during flight-tests). This is
remarkable for a gyro. While under full control, the aircraft can
literally drop-in vertically from any altitude safely.
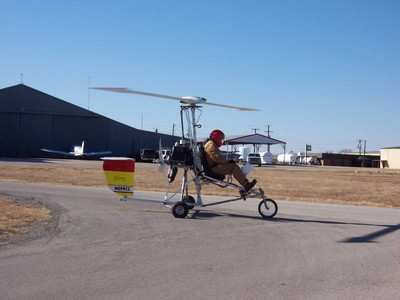
Carter's patented, hollow-blade, composite prop was the next
addition. Its diameter is 60 inches and it produces 325 pounds of
static thrust from 60 HP and yet it weighs only 10.5 lbs with the
pitch change controller. In testing, the Carter prop had a 21%
increase in efficiency for the same hp as the standard kit prop.
Mitchell's report was, "It provides a real kick in the pants for a
very short take-off."
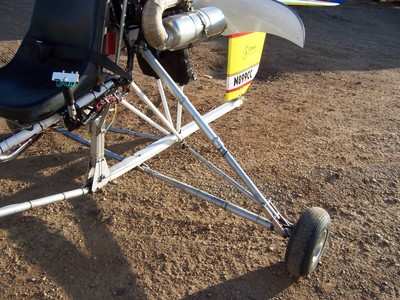
The 26-foot Carter rotor was added to the CGD/T last summer. The
length is the same as the stock rotor although the cord is 2 inches
wider. At that time, Carter expected the new rotor to provide more
than 3 times the lift of the kit's stock rotor giving the CGD/T
jump takeoff capability. To improve the safety of the aircraft and
simplify operation Carter developed a mechanical, rotor pitch
controller. The controller initially holds the rotor pitch flat to
minimize the hp required for take-off. When the pilot is ready for
take-off he engages the controller. From that point on - through
high-speed flight, vertical landing, shut down and the next
vertical take-off - the rotor pitch is completely automatic with no
pilot input. In order to keep the initial take-off Gs down the rate
of pitch increase is also controlled. In addition, to stop the very
high inertia rotor a brake had to be installed. According to
Carter, "The rotor design allows for a tremendous amount of energy
to be stored - about three times the energy per pound of gross
weight of any other rotor system. By developing an automatic
control we have made it simple and safe to manage that energy." A
patent for the new, automatic, rotor pitch change controller is
currently pending.

Carter continued, "We couldn't be happier with the last test
results. We've completed the hours of flight-testing required by
the FAA since the rotor changes were made, but we will continue to
look at the overall safety and response of the systems. There are
still some features that we would like to add like an electric
starter, but we feel the CGD/T can now visually demonstrate that
the age of true personal flight is at hand. We now have a vehicle
that can safely take-off from your driveway, fly 200 miles, and
then safely land and take-off from a truck stop to refuel, or a
restaurant to eat, or a hotel where you can spend the night. The
CGD/T is a mini-Personal Air Vehicle (PAV). It is a glimpse of what
our fully enclosed, 2+2, PAV prototype will be capable of when it
is introduced later this year."
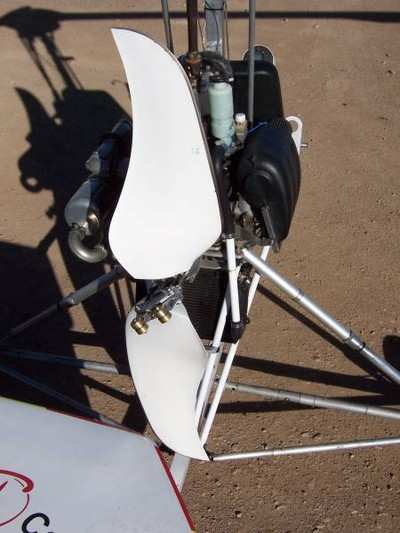
Carter plans to use the CGD/T to publicly demonstrate the
capabilities of their technology and to preview their new Personal
Air Vehicle. The PAV is now scheduled for flight-testing in
mid-2007.