April Tests In Olney, TX, Called A Success
Over the last several days, Jay Carter's wild band of innovators
relaunched the Carter Copter Technology Demonstrator into the air
with a new rotor blade and other significant changes. So far, the
tests seem entirely successful, and Carter engineers are poring
over the test data to see what comes next.
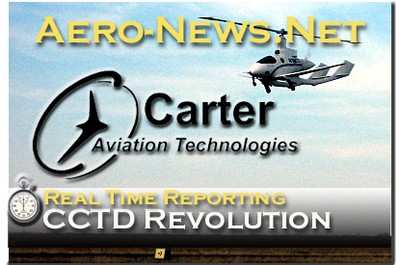
"We're gonna tweak it... it may go faster!" Chief Test Pilot
Larry Neal promised Aero-News. Faster, he meant, than the previous
rotor. And faster, already, than any other gyroplane flying.
The advanced compound gyroplane flew in January and February at
speeds up to 163 mph, before being returned to the plant for work
that included a new rotor, shielded flight computer, and other
systems.
The rotor is the soul of any rotorcraft, even one that is meant
to fly on its wings at high speed, and the newest Carter rotor
incorporates a batch of new ideas. It is longer than the previous
one, and it is easily distinguished visually by its integral
"spinner" or "hub fairing." Less visible to the naked eye, but of
benefit to the durability of the new rotor, the hub also features
integral droop stops. Underneath the fairing, the new design of
rotor has also allowed elimination of the stabilizer bar used on
previous versions.
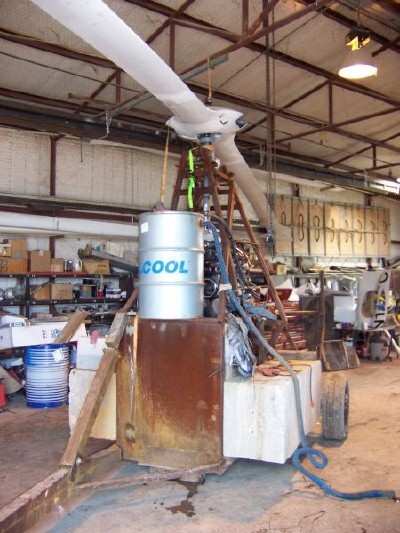
The rotor is constructed of advanced composites with a carbon
fiber spar, as is normal for Carter rotors.
The fairing is not a styling feature; it's meant to help cure a
specific drag problem with the CCTD as the test program explores
ever-higher speeds. While this is the first time the fairing has
ever had physical existence, it's interesting to see that the
earliest design renderings of the CCTD that appeared on the Net in
the 1990s included such a feature. Sometimes life takes a while to
imitate art, perhaps.
Larry Neal praises the new rotor, "Smoother than ever!" and
notes that they are flying consistently at higher Mu values. Mu is
the ratio of reverse flow to forward flow on the retreating blade:
the long-pursued goal for the CCTD is to achieve a Mu of greater
than 1.0, which is literally impossible in conventional rotorcraft,
and has been called "the Mu 1 barrier."
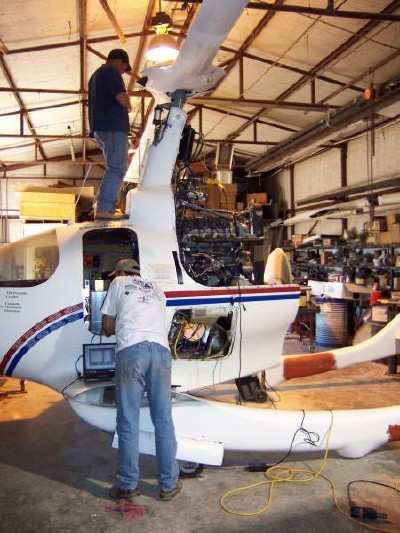
In February with the old rotor they were maxing out in the Mu
0.8 neighborhood, familiar territory for the CCTD. The Carter
engineers are confident that the new rotor will bring the program
to a Mu of 1.3. Larry did not quote specific Mu values; the
engineers are still reducing and reviewing the data.
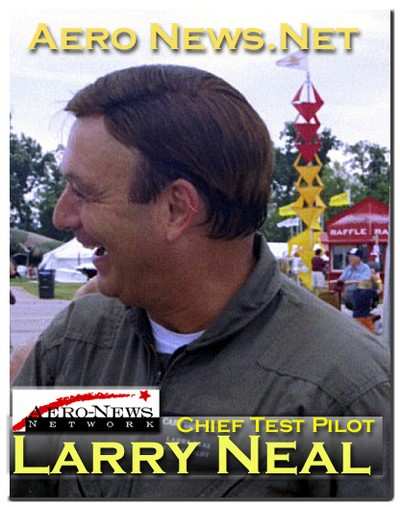
There are some other changes -- the machine's a bit heavier, but
better balanced (no more great wad of ballast in the nose), the
ballistic chute is improved, and the flight control computer has
been shielded against interference. Between the Feb. flights and
these April flights they also made two mods to try to resolve a yaw
condition that was cropping up at high speed (160mph) back in
February. There is no word yet on whether the modifications, a
reduction in rudder area along the trailing edge, and
pilot-controlled rudder locking, somewhat like the tailwheel
locking on large taildraggers, have solved the uncommanded-yaw
problem.
One improvement in the 2005 iteration of the CCTD, which was
already in place for the January and February flights, is in the
propeller. It's got the same GM crate motor putting out
350/380 HP, but the new propeller has made a real difference. The
prop is putting out 1850 lbs thrust vice 1400 on the last one,
which is a pretty significant improvement. The Carter scimitar
propeller is one of the most revolutionary parts of this
unconventional aircraft, combining the rigidity of carbon fiber
with a variable-pitch mechanism that works by applying torsion to
the propeller's spar.
With test pilots Larry Neal and Brad King away at sport aviation
events for the next several weeks, the engineers and technicians
have time to tinker with the CCTD. And the Mu-1 Barrier and the
history books will be waiting when they get back.
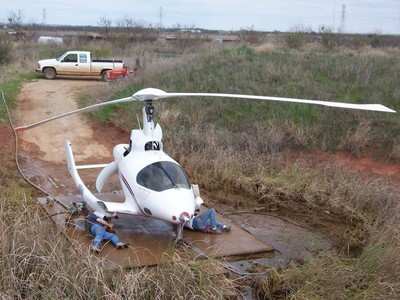
Aero-News thanks Carter Aviation Technologies for the use of
their copyrighted photos in this article.