NASA, Tennessee Students Demonstrate Catch Mechanism For Future
Space Tether
A team of university graduate
students and faculty from Tennessee, with the help of NASA
engineers, have "launched" a subscale spacecraft model and caught
it in mid-air with a unique rendezvous or "catch" mechanism.
Their successful demonstration of this mechanism that could grab
a payload or craft traveling in space marks a critical milestone in
development of a tether-based propulsion system.
The professors and graduate students at Tennessee Technological
University in Cookeville designed, built and recently tested the
subscale tether catch mechanism in a university laboratory.
Tether technology, as potentially implemented in space,
transfers energy and momentum -- called momentum exchange -- from
the tip of a fast-moving, spinning tether to a slower-moving
object, dramatically increasing the object's speed. As the tether
-- a long cable, approximately 60 to 90 miles in length -- spins
end-over-end in space, it catches a payload in low Earth orbit via
a catch mechanism, carries it for a half-rotation, and throws the
payload toward its final destination.
To restore the energy and momentum transferred to the payload,
the tether then uses sunlight collected by onboard solar panels to
drive electrical current through electrically conductive portions
of the tether.
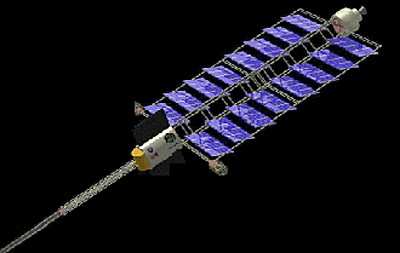
The magnetic field generated by this current pushes against the
Earth's magnetic field and slowly returns the tether to its
original orbit. This technique, called electrodynamic reboost,
restores the tether's momentum and energy, and prepares it for the
next payload. Together, momentum exchange and electrodynamic
reboost are keys to the Momentum Exchange/Electrodynamic Reboost or
MXER tether, an emerging propulsion technology being studied by
NASA.
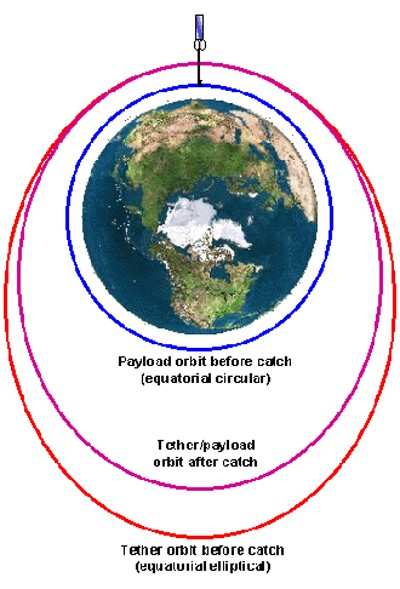
The catch mechanism test project was directed by Dr. Stephen
Canfield, a mechanical engineering professor at Tennessee Tech.
Canfield has investigated tether technology as a faculty researcher
at the Marshall Space Flight Center each summer since 2001, working
with Marshall's In-Space Propulsion Technology Project. In 2003,
Canfield's team and Lockheed Martin Astronautics of Denver, CO,
were both awarded research contracts to develop catch mechanism
designs for tether-based propulsion systems. NASA engineers from
the In-Space Propulsion Technology Office closely participated in
the design and development of the technology.
Canfield's team conducted nearly 50 successful payload catch
demonstrations of the lightweight mechanism -- capable of handling
payloads 10 times heavier than its own weight -- between late
February and early May 2005.
The mechanism caught a free-flying, 25-pound simulated payload,
launched from the floor of a Tennessee Tech laboratory. The payload
was a one-tenth scale model of a generic spacecraft, with a
stabilization gyroscope, batteries, sensors and a camera. While in
a free-fall condition -- similar to the weightlessness of orbit --
the payload was then grabbed in mid-air by the catch mechanism,
which hung from the laboratory ceiling, about 30 feet off the
floor.
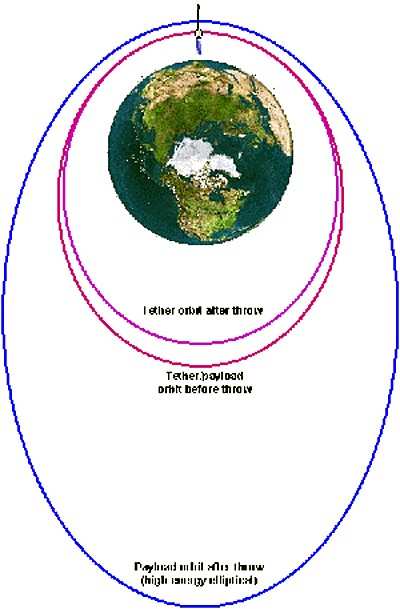
The catch mechanism system uses gravity -- comparable to the
centrifugal force generated by a tether's rotation in space -- to
rapidly close the mechanism's aperture, or opening, around a boom
connected to the payload. During the tests, electro-magnetic locks
called solenoids held the aperture open and then were released to
allow the mechanism to close and capture the payload. The test
sequence accurately simulated the timing and acceleration of a real
space-based tether system -- crucial capabilities for ensuring a
successful catch in orbit. The team plans to conduct additional
tests to demonstrate the use of sensors to automatically trigger
the solenoids. They also intend to test heavier payloads and larger
catch mechanisms.
Tether technology is being developed by the In-Space Propulsion
Technology Program, managed by NASA's Science Mission Directorate
and implemented by the In-Space Propulsion Technology Office at
Marshall. The program's objective is to develop in-space propulsion
technologies that can enable or benefit near or mid-term NASA space
science missions by significantly reducing cost, mass and travel
times.