Space Agency, AFRL Collaborate On Adaptive Compliant Trailing Edge (ACTE) Project
NASA's green aviation project is one step closer to developing technology that could make future airliners quieter and more fuel-efficient with the successful flight test of a wing surface that can change shape in flight.
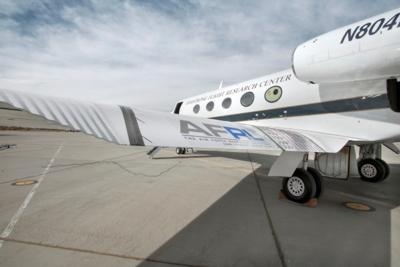
This past summer researchers replaced an airplane’s conventional aluminum flaps with advanced, shape-changing assemblies that form seamless bendable and twistable surfaces. Flight testing will determine whether flexible trailing-edge wing flaps are a viable approach to improve aerodynamic efficiency and reduce noise generated during takeoffs and landings.
The Adaptive Compliant Trailing Edge (ACTE) project is a joint effort between NASA and the U.S. Air Force Research Laboratory (AFRL), using flaps designed and built by FlexSys, Inc., of Ann Arbor, Michigan. With AFRL funding through the Air Force’s Small Business Innovative Research program, FlexSys developed a variable geometry airfoil system called FlexFoil that can be retrofitted to existing airplane wings or integrated into brand new airframes.
FlexFoil’s inventor, FlexSys founder and Chief Executive Officer Sridhar Kota hopes testing with the modified Gulfstream III will confirm the design’s flight worthiness and open doors to future applications and commercialization. ACTE is being flown at NASA's Armstrong Flight Research Center in Edwards, California.
“This flight test is one of the NASA Environmentally Responsible Aviation (ERA) Project’s eight large-scale integrated technology demonstrations to show design improvements in drag, weight, noise, emission and fuel reductions," said Fay Collier, ERA project manager at NASA’s Langley Research Center in Hampton, Virginia.
During the initial ACTE flight, the experimental control surfaces were locked at a specified setting. Different flap settings will be employed on subsequent flights to collect a variety of data demonstrating the capability of the flexible wings to withstand a real flight environment. The flaps have the potential to be retrofitted to existing airplane wings or integrated into new airframes.
“We have progressed from an innovative idea and matured the concept through multiple designs and wind tunnel tests, to a final demonstration that should prove to the aerospace industry that this technology is ready to dramatically improve aircraft efficiency,” said AFRL Program Manager Pete Flick, from Wright-Patterson Air Force Base, Ohio.
ACTE technology is expected to have far-reaching effects on future aviation. Advanced lightweight materials will reduce wing structural weight and give engineers the ability to aerodynamically tailor the wings to promote improved fuel economy and more efficient operations, while reducing environmental impacts.
“The first flight went as planned -- we validated many key elements of the experimental trailing edges,” said Thomas Rigney, ACTE Project Manager at Armstrong. “We expect this technology to make future aircraft lighter, more efficient, and quieter. It also has the potential to save hundreds of millions of dollars annually in fuel costs.”
(Image provided by NASA: For taxi testing on Oct. 31, 2014 at NASA’s Armstrong Flight Research Center at Edwards Air Force Base, in California, the Adaptive Compliant Trailing Edge (ACTE) flap was extended to 20 degrees deflection. Flight results will validate whether the seamless design with its advanced lightweight materials can reduce wing structural weight, improve fuel economy and efficiency, and reduce environmental impacts)