Wed, Dec 09, 2015
Successful On-Engine Tests Of Air Brake System Completed On FJ44-4A Engine
ATA Engineering has demonstrated a novel aircraft drag management device in a series of ground tests performed on an FJ44-4A engine at the Williams International Outdoor Test Facility #2 on October 5–12, 2015. This successful full-scale engine test of a prototype version of ATA’s Engine Air Brake (EAB) demonstrates the technology’s potential to support the goals of NASA and the aircraft industry for next-generation quiet aircraft.
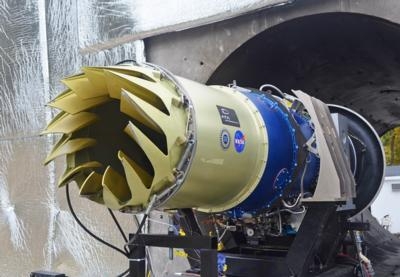
Issues of aircraft noise in the communities surrounding airports have long been a concern; however, developing noise mitigation methods for aircraft without decreasing performance or fuel economy has proven challenging. ATA’s EAB has been designed to address these challenges through the use of a deployable swirl vane mechanism to switch the operation of a turbofan engine nozzle from conventional mode to a “drag management” mode. In this mode, swirling outflow from the thrust-generating exhaust stream allows an aircraft to generate equivalent drag in the form of engine thrust reduction at a fixed fan rotor speed; the EAB thus has the potential to reduce community noise exposure by enabling aircraft to perform descent and approaches slower, aerodynamically cleaner, or steeper (thereby distancing the sound source from the community). But because it stows to be aerodynamically neutral, the EAB does not affect the normal operation of the nozzle during cruise. Moreover, the technology also
has the potential to result in a net fuel burn reduction by reducing the duration of the descent and approach phases of flight.
This recent testing was the culmination of a 27 month Phase II SBIR project sponsored by the Acoustics Branch at NASA Glenn Research Center. However, the development of the patent-pending EAB has been the product of over a decade of research: from an initial concept of a static, ram-air-driven “swirl tube” at MIT, ATA matured the EAB through a campaign of nozzle testing to its current state, with support from the NASA SBIR Program and collaboration with Williams International. This analysis-driven design effort included optimization studies such as steady and unsteady computational fluid dynamics to quantify flow performance and operability, thermal and conjugate heat transfer analysis to predict thermal operating environments, structural dynamics to ensure strength and durability, and computer-aided mechanical design of the deployment mechanism.
The full-scale prototype used in this test was designed to fit within a notional engine cowl of an aircraft using the Williams International’s FJ44-4 mixed-flow turbofan engine, a family of engines that supports business jet customers such as the Cessna CJ4, Hawker 400XPR, and Pilatus PC-24. Future technology maturation efforts will be aimed at further ground testing necessary to demonstrate durability and reliability, and eventual flight testing. Once the EAB is fully proven, it may be used in future designs for quieter aircraft; in the near term, the EAB could also potentially be installed as retrofit equipment on older aircraft engines to meet current and future noise requirements.
With the completion of this successful testing, ATA has also expressed appreciation for the project’s NASA sponsor as well as industry partner Williams International for their invaluable assistance in bringing this technology to fruition.
(Image provided with ATA news release)
More News
Runway Lead-in Light System Runway Lead-in Light System Consists of one or more series of flashing lights installed at or near ground level that provides positive visual guidance a>[...]
Aero Linx: Aviation Without Borders Aviation Without Borders uses its aviation expertise, contacts and partnerships to enable support for children and their families – at hom>[...]
Dave Juwel's Aviation Marketing Stories ITBOA BNITBOB ... what does that mean? It's not gibberish, it's a lengthy acronym for "In The Business Of Aviation ... But Not In The Busine>[...]
From 2010 (YouTube Version): Yeah.... This IS A Really Cool Job When ANN's Nathan Cremisino took over the lead of our Aero-TV teams, he knew he was in for some extra work and a lot>[...]
Also: Junkers A50 Heritage, Montaer Grows, Dynon-Advance Flight Systems, Vans' Latest Officially, the Carbon Cub UL and Rotax 916 iS is now in its 'market survey development phase'>[...]