NTSB Releases Probable Cause Report, Two Fatally Injured
The NTSB has released its probable cause report from an accident which occurred in January, 2015 that resulted in the fatal injury of two people on board an Enstrom 280FX helicopter. The board said on of the three main rotor blades on the aircraft separated from the rotor head, leading to the accident.
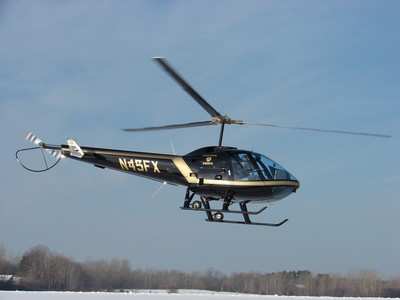
According to the report, the flight instructor and the student pilot were conducting a local instructional flight in the helicopter. The helicopter was on final approach to land when one of the three main rotor blades (#2 blade) separated from the main rotor head. The main transmission and main rotor head (with #1 and #3 blades still attached) then separated from the helicopter, and the helicopter descended to ground impact. Examination of the wreckage revealed that the separation of the #2 blade was due to fracture of the #2 main rotor blade spindle.
The #2 spindle fractured at the inboard end of the threads. Metallurgical analysis of the fractured spindle revealed signatures consistent with a fatigue crack initiating from multiple origins that propagated across 92% of the spindle cross-section; the remaining 8% of the fracture surface exhibited signatures consistent with overload. The high percentage of stable fatigue fracture growth versus overload suggested that low loading propagated the crack.
Further, corrosion was visible on the fracture surface in the fatigue initiation area, which indicated that the crack had been present and growing for some time. Similar fatigue cracks were observed emanating from thread roots on the #1 and #3 spindles; the crack in the #3 spindle emanated from the inboard-most thread, similar to the crack in the #2 spindle, and the crack in the #1 spindle emanated from the cotter pin hole. Both of these cracks were shorter than the crack in the #2 spindle, and the fatigue on their fracture surfaces had only propagated a small amount through the #1 and #3 spindle cross-sections.
The root radii of the threads on all three of the spindles did not meet the thread form specified on the manufacturer's drawing. Cross-sections of the threads from the three spindles showed that the #2 spindle and the #3 spindle had flat-bottomed threads; the #1 spindle did not have flat-bottomed threads but had threads with a sharper than specified root radius. A subsequent finite element analysis determined that the flat-bottomed threads and the sharper than specified root radius threads would result in higher stresses at the threads, which likely contributed to the crack initiation within the threads.
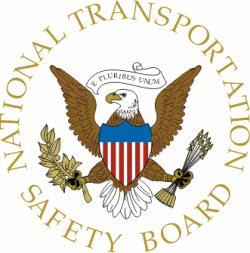
Further, the investigation determined that the predicted loads used in the original fatigue analysis during the design of the spindle did not account for a bending load at the spindle threads. The omission of bending loads during design and the flat-bottom quality of the threads led to stresses greater than used in the original fatigue life calculation by the manufacturer. Further, the finite element analysis of the spindle revealed that, once a crack has initiated, the bending loads at the spindle threads would be sufficient to propagate the crack at a rate similar to that of the total time accumulated on the #2 spindle (about 9,300 flight hours).
Before the accident, the spindle was not a life-limited part, and there were no recurrent inspections specified for the spindle threads, resulting in a low likelihood of the operator detecting the fatigue fracture within the spindle threads before the accident. Following this accident, the manufacturer released a service directive bulletin and the Federal Aviation Administration released an airworthiness directive that require a magnetic particle inspection of spindles with 1,500 hours or more time in service.
The NTSB determined the probable cause of this accident to be an in-flight failure of the helicopter's #2 main rotor spindle due to undetected fatigue cracking, which resulted in an in-flight breakup. Contributing to failure were the nonconforming thread root radius of the spindle and the manufacturer's failure to include a bending moment within the spindle threads when performing the fatigue analysis during initial design of the spindle.
(Image from file. Not accident aircraft)