Airplane Banked “Hard” To The Left, Pitched Nose Down And Descended Into One Of The Power Lines
Location: Charlestown, NH Accident Number: ERA21LA283
Date & Time: July 10, 2021, 18:13 Local Registration: N346FL
Aircraft: Bailey N Moyes Dragonfly Injuries: 1 Fatal, 1 Serious
Flight Conducted Under: Part 91: General aviation - Personal
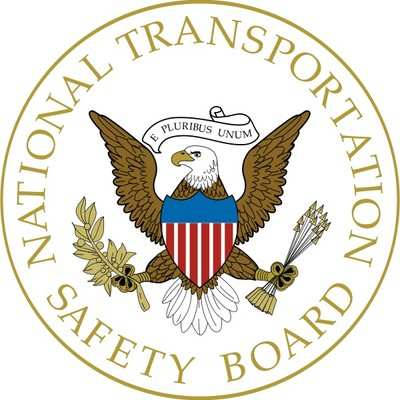
On July 10, 2021, at 1813 eastern daylight time, an experimental light sport Bailey Moyes Dragonfly, N346FL, was substantially damaged when it was involved in an accident at the Morningside Flight Park, Charleston, New Hampshire. The commercial pilot sustained minor injuries. The pilot-rated passenger was fatally injured. The airplane was operated as a Title 14 Code of Federal Regulations (CFR) Part 91 personal flight.
According to the pilot, prior to the accident flight both he and the pilot-rated passenger performed a preflight inspection together. After the inspection, the pilot-rated passenger flew the airplane solo and performed three touch-and-go landings. After that flight the pilot-rated passenger stopped the airplane, moved to the rear seat, and the pilot sat in the front seat and performed one touch-and-go and one full stop landing. During the third circuit in the traffic pattern, while on final approach, the airplane was too high and the pilot-rated passenger told the pilot to perform a go-around, which he did. During the subsequent downwind leg, the engine power was set initially at 4,200 rpm. Near the end of the downwind leg, at an estimated altitude of 400 ft above ground level, the pilot-rated passenger shook the control stick “violently” and yelled “something about ‘power.’” He shook the controls again and yelled “my airplane” and assumed control of the
airplane. At that time the pilot noticed that the engine speed was about 3,200 rpm, slightly below the typical level cruise flight value of about 3,500 rpm. As the airplane was abeam the runway threshold with the engine rpm about 3,200, the pilot-rated passenger began a turn towards the base leg of the airport traffic pattern. At that time, the front seat pilot noted that the airplane was “low” but he thought the altitude was sufficient to clear the power lines. During the turn the engine “lost partial power” and the airplane banked “hard” to the left, pitched nose down and descended into one of the power lines. After the airplane impacted the ground, the engine continued to operate. The pilot attempted to shut down the engine with the magneto switches, but the engine continued to run. He then located the master switch, turned it off, and the engine stopped.
The power lines were oriented generally north/south (about 005° magnetic) and located between 350 to 500 ft west of the runway (which was oriented about 14° magnetic; the takeoffs and landings were all to the north). The towers were about 350 ft apart, and the highest wire was equipped with visibility marker balls (2 balls spaced along the wire between each tower).
Examination of the airplane by a Federal Aviation Inspector revealed that all major components of the airplane were present at the accident site. The airplane came to rest adjacent to one of the utility towers supporting the power lines. An electrical arcing mark was present on the left wingtip. The forward fuselage was fractured aft of the front pilot station and was mostly separated from the remainder of the fuselage. The airplane was mostly intact from the rear pilot station to the tail. The aileron and rudder controls were continuous from the rear pilot station to their respective control surfaces. The elevator controls were continuous from the rear pilot station though a fracture in the elevator push-pull tube (which remained attached to its fixtures at both ends), to the elevator. The airplane was equipped with an airframe parachute, which was not deployed. The “safety pin” which prevents accidental deployment while on the ground, was removed (which is appropriate for flight). The
fuel tank was about ½ full, a sample of fuel taken upstream of the fuel filter appeared and smelled consistent with automotive fuel (which is the engine manufacturer’s recommended type of fuel). The tips of all three composite propeller blades were frayed/damaged. The engine throttle control cable was fractured in several locations.