Carter Tests Propeller Design for UAVs
One of the things that makes the CarterCopter successful is its
efficient use of power. Even though its motivation is
Corvette-based, the job the engine is asked to do is a big one:
break the Mu-1 barrier. That meant to Jay Carter that the propeller
for his gyroplane had to be the best-possible thrasher of air. So,
Jay invented a radical new prop.
After a Sun 'n Fun presentation a year ago, ANN's
recip engine man, Tim Kern, and CarterCopter genius Jay Carter were
talking about the possibilities for some of the new technology
embodied in the CarterCopter, and Tim suggested licensing the
prop's qualities, separately, for applications that weren't the
CarterCopter's own. Well, it's better: Carter is making the props
himself. Here's a new press release:
Carter Aviation Technologies, best known for their revolutionary
gyroplane technology, is expanding their sphere of development. It
is being announced that Carter has designed, built, and bench
tested a composite prop with matching spinner to be used on an
Unmanned Aerial Vehicle (UAV).
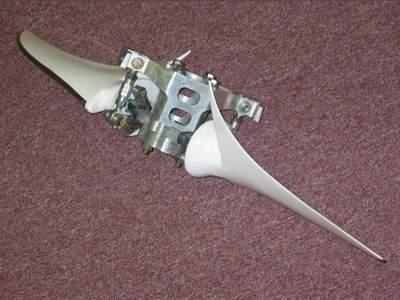
Carter’s new UAV prototype propeller is 28” in
diameter with a 9” spinner. Although the 8’ version of
the Carter design prop has been flying very successfully on their
prototype gyroplane since 1998, the development of this new
diminutive prop required new tooling, molds, testing
instrumentation -- and the same amount of engineering effort as the
original propeller. This development project was completed in
record time due to the long hours put in by Carter engineers and
technicians.
Stan Clines, Composite Specialist, was in charge
of the prop production, Kenneth Hibbs, Electronic Specialist,
handled the instrumentation and Mark Robinson, Machinist and
Mechanical Technician, built the test stand and readied the prop
for testing. Jay Carter, Jr., President and Chief Engineer, headed
the overall testing sequence. Bench testing of the prototype began
during the first part of January 2003. Testing requirements called
for the prototype prop to be bench tested at a tip speed exceeding
Mach 1 for a minimum of 10 minutes to prove its strength and
durability.
On January 29, 2003, the new prop was tested for the required 10
minutes at 8600 rpm where the tip speed exceeded the speed of
sound. Each 4/10 lb blade produced 7400 lbs of centripetal force
when the blade tip exceeded Mach. This initial testing also showed
that there was a 15% reduction in horsepower required at 7000, rpm
when compared to a wood prop currently used on a UAV. Testing will
continue. In addition to testing for greater efficiency, Carter
will be looking at the noise reduction advantage estimated for
their prop.
Jay Carter noted, "This is an extremely important step for
Carter. It marks the first time that our patented technology will
be focused on a use outside of our own company. We had to develop
several different technologies to support our work in gyroplanes. A
new, highly efficient, low-cost, lightweight propeller was one of
our goals. A unique quality of our propeller design is that it is
fully scalable and highly efficient in either a tractor or pusher
configuration. Also, with minimal structural, mechanical,
static/dynamic, aero-elastic or shape limitations our design allows
the prop to be shaped for maximum airflow efficiency."
This announcement suggests that a relatively
low-cost, lightweight, retrofitted prop can increase the flight
efficiency of a production UAV system by a significant percentage.
The new prop features ground-adjustable pitch, low inertia due to
its lightweight construction, metal abrasion weather strip on the
leading edge, and an ideal planform (large chord at blade root)
that improves prop efficiency. If the new Carter prop continues to
test as well as it did initially, then every manufacturer of a
prop-driven UAV could retrofit this same type of prop.
Carter continued, "To some degree, our propeller technology is
an extension of my years spent in engineering wind turbines to
garner efficient air movement. It is gratifying that these new
propeller tests are beginning to prove our development theories. I
believe that our propeller design, when fitted to a specific
engine, could improve prop efficiency from 10% – 20% over
many other propellers in use today. Plus, our extremely lightweight
design provides a high safety factor and with the blade’s
flatwise flexibility, gyroscopic loads into the engine and airframe
are greatly reduced. This would be a marked improvement for the
general aviation industry."
[Hey -- I just got an idea: could your airplane use 10~15%
better prop efficiency, quieter running, and possibly lower prop
maintenance?]